 |
| | 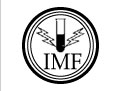 |
 |
 |
|
|
ANODISING
Introduction
Anodising is an electrochemical technique most usually applied to aluminium and its alloys. These are treated to form a structured surface oxide layer. This layer has anti-corrosion and decorative properties. The anti-corrosion properties are optimised by a post-anodising process of "sealing".
The anodising techniques applied on aluminium are divided into:
- Sulphuric acid-anodising,
- Hard anodising,
- Chromium acid anodising.
|
|
Anodising of aluminium is frequently applied. Since the anodised layer is thin and transparent, surface damage and scrapes are easily visible. Before anodising aluminium components must be treated carefully in order to prevent damage. |
Aluminium anodising: properties
The layer thickness of an anodising layer made in a (standard) sulphuric acid anodising bath can be selected to be between 1 and approx. 30 micrometer.
Hard anodising gives layers of approx. 5 up to 100-150 micrometer thick (dependent of the type of hard anodising bath). The layer grows partially (approx. 60%) out of the substrate so that an anodising layer of 20 micrometer will give rise to an extra thickness of the component of 8 micrometer.
Hardness |
250-450 Hv 0,1 |
Adhesion |
Better than standard galvanic coatings |
Ductility |
Low, essentially the anodising layer is a ‘glass’ layer |
Electrical Resistance |
An anodising layer is a good isolator |
Anodised aluminium can be given many different colours. If coloured with inorganic dyes, they show very reproducible and stable colours (organic dyes are less stable).
Sulphuric acid anodising treatment strongly reduces the fatigue strength of aluminium so that this process is less suitable for components subjected to fatigue. Chromium acid anodising is better suited for fatigue resistance applications. Anodising layers are also suited as substrate for adhesive or for organic top layers. They are not very resistant to hydrogen fluoride containing cleaning products. Also strong alkaline solutions and acids attack anodising layers. The corrosion resistance of sulphuric acid anodising layers is caused by sealing of the pores with aluminium hydrate.
If components are not seriously polluted, the sealing of the pores (which is strengthened and restored by moisture) remains active for dozens of years.
More information
More information can be found in:
The surface treatment and finishing of aluminium Alloys - S. Wernick, R. Pinner and P.G. Sheasby
ISBN 0-904477-09-6
Also from the Aluminium Finishing Association (www.alfed.org.uk) which deals with powder coating, architectural and strip anodising.
|
|
Substrate material
In general, all wrought aluminium alloys can be anodised. A high zinc or copper alloy composition may cause problems due to inferior anodising thickness. High silicon alloys such as in cast aluminium give rise to a black anodising layer with often only moderate technical properties. Anodising layers on zinc are in general black.
On titanium pastel colours can be obtained, depending on the applied process. The colour of anodised magnesium is similar to that of aluminium. |
Hard anodised engine components of cast aluminium.
Aluminium anodising: Process characteristics
If an electric current is conducted through an electrolyte solution in which an aluminium article is made anodic, an oxide layer is formed, which isolates the underlying metal.
In order to ensure a continuous formation of the oxide layer, an acid is added to the aqueous solution. This acid causes pores to be formed in the oxide so that electric contact and the discharging of the of anions can continue. Acids used are sulphuric acid, chromium acid, phosphorus acid and oxalic acid.
|
|
(Dark coloured anodised aluminium fencing)
Sulphuric acid anodising in generally is carried out at approx. 18 °C. The higher the temperature the higher the dissolving rate of aluminium in the acid. At increasing temperatures the formation rate of the oxide layer decreases, and the pores get larger. |
Good colourability with organic dyes requires relatively large pores and a somewhat higher anodising temperature (approx. 22°C).
|
|
(Hard wear resistant anodising layers are used for moulds):
Hard wear resistant layers should be thick with relatively small pores. Hard-anodising is thus carried out at -2 to -5°C. As an after treatment sulphuric acid anodising layers are sealed. In general sealing is carried out in overheated steam or in almost boiling de - ionised water. |
|
|
(Left is an open sealing tank. In order to prevent heat losses sealing tanks are closed with isolating lids):
In the pores aluminium hydrate is formed, which has an approximately 7 times higher volume than the aluminium. Because of this the pores are sealed with aluminium hydrate. If during the life span of the anodised component the aluminium hydrate is removed, the presence of condensed water is sufficient to get the aluminium hydrate formation starting again, thus restoring the original corrosion resistance. |
Pre-treatment
|
|
(Pre-treatment of aluminium profiles. The profiles are suspended after pre-treatment in order to drain): Because normal anodising layers are transparent and colourless, pre-processing is very important, e.g. grinding, polishing or brushing.
Etching is carried out in sodium hydroxide, which also degreases. During this alkaline etching the aluminium dissolves. However, alloying elements such as silicon and copper stay behind in the form of smut low on the surface. This smut is removed by a ‘desmut dip’ containing nitric acid and hydrogen fluoride.
|
Order of pre-treatment:
- Mechanical processing (grinding, brushing, polishing)
- Etching in alkaline solution, including degrease
- Desmutting
Aluminium anodising
Anodising is carried out in electrolyte containing sulphuric acid or chromium acid. With a direct current source an amperage is introduced of 1-2 A/dm2, typical anodising times with sulphuric acid anodising are up to 60 minutes.
|
|
The whole fluid surface moves, caused by the bath agitator. This movement is necessary to maintain an even temperature in the bath.
Baths are also cooled.
The metal bar makes contact at the side of the bath with the electric wiring linked to the rectifier. The products to be anodised are connected to this bus - bar. |
After-treatment.
After anodising the components are rinsed in very clean water for a considerable amount of time so that all electrolyte can diffuse out of the very small pores (osmosis) Before sealing the anodising layer may be coloured.
|
|
Rinsing bath. For intensive rinsing the fluid is constantly stirred.
Colouring is done in several ways. Inorganic dyes such as tin are deposited in the pores by a galvanic process. They form metal oxides in the pores whose colour effect can range from light bronze to dark bronze and from yellow to blue. These colours are stable in daylight. |
|
|
The new cathedral of Lichen in Poland. In the years 2000 and 2001 this new building was given gold coloured anodised aluminium front elements.
Before anodising the components were polished. |
|
|
(Bronze coloured anodised lamp post.):
All possible colours are introduced into the pores by water soluble organic pigments. After rinsing the layer is condensed by sealing in hot water (96 °C) where a minute of sealing time per micrometer layer thickness is needed.
Local colouring is used to produce images in the anodising layer. This is done by screen printing. Even photograph can be reproduced in this way into the anodising layer. |
Advantages and disadvantages
Advantages: Anodising layers have an exceptionally long life span in outdoor applications assuming they are not subject to pollution. Anodising layers do not limit the recyclability of the anodised aluminium.
Restrictions: sulphuric acid anodising layers are brittle and as a result cannot be deformed very well. Anodising layers coloured with organic dyes can discolour after a certain time under the influence of sunlight.
Applications
|
|
Anodised aluminium is applied on a large scale for window frames, building facades, ornaments etc.. The anodising layer is hard and wear resistant as well as very resistant to corrosion. If the building facades are regularly cleaned with non aggressive cleaning agents the life span of the anodising layer is extremely long: a life span longer than 40 years is no exception. |
|
|
Sailing ship, mast anodised with sulphuric acid, colour natural. From the Netherlands.
|
|
|
Anodised masts for yachts are commonly applied because of the good wear and corrosion resistance in maritime environment. |
|
|
Hard anodised components in several colours.
This technique gives good wear resistance.
Hard anodised aluminium is applied on cylindrical axles, machine parts and in general components which need a hard and wear resistant surface. Anodised aluminium is used on a large scale in electric condensers and as printing plates in offset printing. Because the anodising layers are easily coloured with dyes, anodised components can easily provide coloured images in a production line. |
|
|
Anodised plate for a money machine. Sieve printing is used to bring dyes into the pores of the anodising layer, after which the pores are sealed. |
|
|
Infra-red measuring probe.
Black coloured anodised aluminium on which electrolytically gilded reflectors have been mounted. The assembly holes are chromated. Such measuring probes are applied in satellites for scientific research. |
Chromium acid anodising is used for aluminium components which are subjected to fatigue, such as plane components, and for components which must be glued. The adhesive connection on a chromium acid anodised surface is much stronger than directly on aluminium. Chromium acid anodising layers are grey to light yellow/green. Sulphuric acid anodising layers are colourless. Since an anodised layer on wrought aluminium alloys is in fact an almost colourless glass layer defects of the substrate, such as scratches, remain visible.
|
|
Anodising layers are colourless but can be coloured. A well-known application are door latches and the metal-work, of doors. |
|
|
Coilcoat installation. In such installations aluminium coils are anodised or lacquered.
Anodised coils are used for offset plates and in the caravan industry (Coilcoat). |
| 
|
| 
|

|

|
|