 |
| | 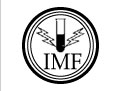 |
 |
 |
|
|
CHEMICAL NICKEL
Chemical Nickel – Properties
The surface properties are almost independent of the base material. The layer follows the surface geometry. Proper thermal after-treatment can increase the hardness and wear resistance.
 |
|
Low P Nickel is relatively hard and magnetic.
Middle P Nickel is less hard, but gives reasonable corrosion protection, and as a result is applied most often. This layer shows weak magnetic properties.
High P Nickel is very corrosion resistant, and not magnetic |
Chemical Nickel - Process
Chemical Ni can be deposited on;
- steel and stainless steel
- cast iron and cast steel
- copper and copper alloys, both on extruded, cast and heat pressed parts
- aluminium and aluminium alloys, both on injection moulded, cast and extruded parts
- zinc injection moulded parts
- plastics (among others ABS and polycarbonate)
Process characteristics
Chemical nickel is deposited in an aqueous solution of a nickel salt and a reducing agent at 85 to 95 °C. On plastics the chemistry is adjusted to a working temperature 60 to 75 °C.
We discriminate between
Ni containing 2 to 5% P (low)
Ni containing 6 to 9% P (medium)
Ni containing 10 to 14% P (high)
Composite layers with PTFE (Teflon), silicon carbide (SiC) and diamond particles are also deposited.
Pre-treatment
|
|
Mechanical pre-treatment for removing an oxide layer or to provide a desired final appearance may involve polishing, glass or sand blasting.
Pre-treatment depends on the type of base material. The products are always (electro) chemically cleaned and activated before deposition. |
Layer deposition
This takes place over the entire surface. Surface roughness is determined by the base material. Thick layers could have a higher surface roughness. Partial deposition is possible (by covering part of the surface).
|
|
There is uniform covering over edges, through holes can be coated if the plating solution can be continuously refreshed. Layer thickness up to 200 µm is possible.
A thickness of 2 to 50 µm is usual on plastics up to ± 1.5µm.
Deposition rate is 8 to18µm/h.
Adhesion strength on steel and copper is 345 to 441 Mpa; on aluminium 103 to 241 MPa. |
After-treatment
Thermal after-treatment (increase of hardness and wear resistance) is carried out at a temperature of 200 °C to 400 °C for 10 to 24 hours. For reduction of hydrogen brittleness annealing up to 240 °C may be required, dependent on the alloy composition of the steel substrate.
Advantages and disadvantages
Advantages;
- Dimensional stability of the product (no edge building, and homogeneous thickness distribution)
- The coating can be applied onto almost any material, designers have many options
- Good corrosion resistance
- Good resistance to abrasive wear.
Limitations;
- low ductility of the layer
- wear resistance is somewhat lower than that of hard chrome
- some limitations to the geometry of the part to be coated
- less uniform growth in through holes
- maximum temperature during use (with constant functional properties of the layer) is around 320°C.
Costs
Costs are dependent on pre- and after-treatment, layer thickness and additional requirements
???? no figs
Figure 1 to 4;
Chemical Nickel – Application
Chemical nickel is often applied on parts with a complex geometry. Exact dimensions can be attained by tuning the uniform layer thickness.
Applications;
Machines and Equipment; protection against wear and corrosion
Automobiles: Parts in carburettors, injection systems, and the ABS system. The aim is always corrosion and wear protection, and thermal conductivity.
Offshore: Thick layers for corrosion protection in (sea) water environment
Chemical industry: Process parts, reactor vessels, etc. for chemical resistance
Aerospace: Connection between solar panels and satellite. Corrosion resistance and high strength.
Electronics: EM shielding and solderability
Moulds: As top layer or intermediate layer for a PVD (e.g. DLC) coating. As an intermediate layer the function is to ‘bridge’ the hardness, and increase adhesion.
Chemical copper
Chemical gold
| 
|
| 
|

|

|
|