 |
| | 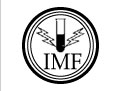 |
 |
 |
|
|
COMPOSITE COATINGS
Introduction
Composite plating, also called dispersion plating, is an electrochemical surface treatment technique, which covers the surface – after proper pretreatment – with a metallic layer in which the dispersant is homogeneously incorporated.
The layer synergistically combines the interesting properties of both phases. This means that the properties of the composite layer are better than the properties of the constituent parts.
NO PIC
Figure 1
Surface of a layer including SiC particles
V=7500 x
Composite layers, also called dispersion layers, are coatings consisting of two or more phases with a metal matrix and a hard phase as dispersant in the matrix. Often chemical nickel is selected as the matrix phase; more rarely electrodeposits can be used. Examples of dispersants are;
- carbides, nitrides, borides
- diamond
- dry lubricants such as PTFE, MoS2, graphite
The schematic build - up of a composite layer. The layer thicknesses are tentative.
Chemical Nickel-SiC (silicon carbide)
The surface properties are almost independent of the base material. SiC is homogeneously disposed in the matrix, which ensures constant properties. Sharpness and dimensions remain very constant, even in the micron regime. Machining of these layers is most often not needed.
The layer thickness of the chemical Nickel-SiC layer is between 10 to 50 µm. The layers have a low friction coefficient when lubricated.
The layer hardness varies between Hv0,1 70 kg/mm2 to Hv0,1 1250 kg/mm2. The layers have a good heat conductivity.
Picture of a composite layer. The dispersed SiC is visible in the Ni matrix. V=500 X.
Chemical Nickel-PTFE
PTFE is homogeneously dispersed in the matrix, enabling constant properties. During frictional applications, the PTFE sticks to the adhering material, thus preventing adhesive wear by cold welding.
Sharpness and dimensions remain very constant, even in the micron regime. No machining is necessary.
The layer thickness of a chemical Nickel-PTFE layer varies between 5 and 15 µm.
The friction coefficient is low.
The layers have good heat conductivity and good anti-sticking properties.
The layer hardness varies between Hv0,1 300 kg/mm2 to Hv0,1 500 kg/mm2, depending on after treatment.
Can be used in practice up to 200 °C.
Substrate
The composite layer can be deposited on ferrous and non-ferrous metals.
Chemical Nickel-SiC and chemical nickel - PTFE
Depending on the application, the substrate may be sand blasted, or machined and polished.
Process characteristics
Layer deposition is carried out in an aqueous solution of a nickel salt, a reducing agent and the PTFE or SiC dispersion, at a temperature of ± 85 to 95 °C. The deposition time depends on the desired layer thickness.
Growth rate incorporating PTFE is typically 5 to 10 µm /hour and for SiC 10 to 15 µm /hour.
Pre-treatment
Chemical Nickel-SiC
In most cases machined surfaces are used
Chemical Nickel-PTFE
Mechanical pre-treatment such as sand blasting, machining and polishing is possible for functional and aesthetic reasons.
Electrochemical pretreatment is always dependant on the composition of the base material, and usually consists of degreasing, cleaning and activating the surface.
Layer deposition
The layer is deposited over the entire product surface. Often an underlayer of chemical Ni is to ensure good used adhesion and for extra corrosion protection.
It is possible to cover part of the surface to prevent layer deposition. Product corners usually give uniform deposition. Also the inside of through holes will be covered. There is no deformation as result of higher temperatures during deposition.
The surface roughness of chemical Ni-PTFE is somewhat lower than that of the base metal.
The surface roughness of chemical Ni-SiC is somewhat higher than that of the base metal, as a result of the sharp SiC particles.
After-treatment
Chemical Nickel-SiC
The hardness of the layer is Hv0,1 700 kg/mm2 and can be increased to Hv0,1 1200 to 1300 kg/mm2 by thermal treatment (300 °C).
Machining is often used in order to get a more uniform and better wear resistant surface.
Chemical Nickel-PTFE
The hardness of the layer is Hv0,1 300 kg/mm2 and can be increased to Hv0,1 300 to 450 kg/mm2 by thermal treatment (300 °C).
When treating deposits on aluminium and its alloys the maximum temperature of the substrates should be taken into account. Also the anti-sticking properties improve: the PTFE particles near and at the surface are ‘sintered’. The hardness of the layer is relatively low due to the presence of 20 to 25 vol% PTFE; for most applications however this is sufficient.
Advantages and disadvantages
Advantages;
- As a result of the high dimensional accuracy and homogeneous layer deposition It is possible to obtain very exact fittings.
- High mechanical strength of the layer
- Many forms can be coated
- Chemical Nickel-PTFE exhibits good dry lubrication and anti-sticking behaviour.
- High strength of the coating compared to sealed systems
- Chemical Nickel-Sic exhibits very low wear and friction coefficient, lubrication by a very well adhering oil film
Limitations;
Chemical Nickel- PTFE; as result of the low ductility the layer has limited strength in local loading situations. As a result of the good anti-sticking properties glueing is impossible.
For chemical Nickel-SiC; special electroplating baths are used (because of the complicated bath movement needed). This can cause limitations to the size and shape of parts to be coated.
Composite Layers – Applications
Deposition is possible on both large and small parts larger parts treated in small containers. Almost any conducting base material can be coated. The coating can also be deposited on hardened and/or high-alloy steels.
Chemical Nickel-SiC
Chemical Nickel-SiC surfaces retain a stable oil film, so that application in motors is possible. Sometimes the layer is applied on moulds for injection moulding when a shiny appearance of the (hardened) plastic material is not required.
The layers can be used for increasing the abrasive wear resistance of a part. Also applicable on steel and stainless steel alloys. Many applications can be found in packaging, e.g. on metal clips and on ducts.
Two stroke engine in model building. ‘Wankel’ engine.
Chemical Nickel-PTFE
Chemical-Nickel-PTFE is used as a non-adherent layer in the injection moulding of plastics. The layer is also used for increased wear behaviour on aluminium and brass parts. This coating is also applicable on steel and stainless steel alloys.
The layer is used on air bearings for (dry) lubrication.
Many applications are in packaging and transport systems (for friction reduction).
Gas seals as applied in camping gas bottles, coated with Chemical Ni-PTFE.
| 
|
| 
|

|

|
|