 |
| | 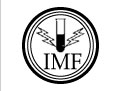 |
 |
 |
|
|
DECORATIVE CHROME PLATING
1. Introduction
To produce decorative chromium plating, the parts to be coated are made the cathode within an electrolytic cell which contains inert (insoluble) anodes and a solution containing chromium salts. Metallic chromium is deposited using direct current. A water based solution of chromic acid is used. Other special additions are used to increase the efficiency of the bath and produce an even, bright deposit on the surface of the part. To produce the bright, reflective finish commonly associated with decorative chromium finishes it is important to ensure the surface being coated is also bright. Chromium is commonly deposited onto a bright nickel surface to achieve this type of finish. Other metals or finishes on the layer below the chromium can be used to influence the appearance of the chromium layer. Both bright and semi - bright layers are possible depending upon the finish beneath the chromium layer. An alternative process for decorative chromium plating uses a less toxic electrolyte based on trivalent chromium salts.
2. Properties
Chromium layers are hard wearing and very corrosion resistant in most environments.
In daylight, bright chrome has a silvery bluish reflection. The corrosion resistance of the chromium layer is due to the formation of a thin chromium oxide surface layer in air. This oxide layer gives the chromium a tarnish resistance similar to that of stainless steel.
|
Chrome plated tools |
3. Substrate
Products which are often chromium plated are made from steel, brass, zinc and some grades of plastic.
Specific pretreatments are necessary for the respective substrates.
4. Process characteristics
Hexavalent chromium baths for decorative finishes operate most efficiently between 250 and 400C, and they contain solutions with around 250-350 g/l of chrome VI salts. The solutions are extremely acidic and oxidative. They are aggressive to the plating equipment, the environment and the operators of the process. Hence the plating activity needs to be expertly managed.
Pretreatment
Prior to decorative chromium plating the original part must be thoroughly cleaned and degreased. Defects on the component surface or in layers plated prior to chromium will result in a poor aesthetic finish with severely reduced corrosion resistance. Care must be exercised to ensure that any underplate (e.g. bright nickel) is activated for the chromium deposition.
Layer deposition
For decorative applications a layer of chromium with a thickness of 0.2 to 0.5 µm is the industry standard. Less than this the layer may not be continuous, above there is a risk of the layer becoming cracked. Macrocracking
The nickel under plate can be varied to produce either microporous chromium layers or microcracked chromium.
These deposits are used for specialised surfaces and particular environments. (see ISO 1456; ISO 4525.2)
Although chromium deposits are themselves extremely corrosion resistant, the overall protection offered by a bright plated finish is a combination of the properties of the chromium layer and the under layers.
|
|
A decorative layer in cross section. |
At the bottom of the picture the steel matrix being coated can be seen; above this is an underlying thick dull nickel layer; above this again is a bright nickel layer, characterized by its lamellar structure. This combination of layers provides an enhanced corrosion resistance. On top of all this is a thin chromium layer, approximately 0.2- 0.3 µm thick.
5. Advantages and disadvantages
Advantages
- Very corrosion resistant, scratch and wear resistant, and colour stable. The layer is also heat resistant, dirt resistant and easy to clean.
- Chromium has an attractive bluish appearance and retains the brightness of the underlying nickel
|
|
Decorative top coating on a copper part. By variation of the brightness of the underlying nickel many different effects can be obtained. |
Limitations
- Thin decorative chromium is usually not crack or pore free
- Due to this the underlying nickel may be attacked by corrosion
- Barrel plating is not usually possible
- The maximum layer thickness is low, after which the brightness is lost
6. Applications
For example: -
- Household products
- Kitchen and bathroom products
- Sanitary products
- Automotive products
- Design furniture.
- Hospital equipment
- Light alloy products, subject to wear
|
|
Tap with decorative chrome (Thick nickel and very thin chrome layer) |
Decorative chromium is always deposited as a thin layer (0.2 to 0.4 µm) mainly onto nickel plated parts for the preservation of a bright appearance.
|
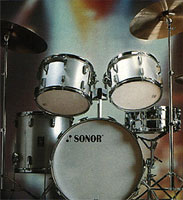 |
Application of decorative chrome in automotive industry |
Drums with decorative chrome |
7. Trivalent chromium processes
It is now possible to deposit thin chromium layers as a decorative finish from trivalent chromium chemistry baths. This is a much more benign process than the conventional. However the process is self limiting, so thick microcracked layers cannot be produced.
The operation and expertise in the use of trivalent chromium plating baths has matured to a point where the two processes are interchangeable. The deposits produced from either type of bath will produce corrosion resistant decorative finishes suitable for most environments.
| 
|
| 
|

|

|
|