 |
| | 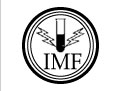 |
 |
 |
|
|
ELECTROFORMING
Introduction
Electroforming is defined in ISO 2080 as the fabrication or reproduction of parts by electrodeposition on a mould, after which the deposited metal is detached from the mould and used separately.
The electroforming of parts is a well established technique. In this way copies of precious products, such as antique coins and jewels, also of natural products, such as beetles, leaves etc. are made.
The technique of electroforming has seen an strong increase in use over the last decades, with an emphasis on technical applications such as moulds, electronic components, and for screen printing. (Link to p 86)
Electroforming enables the exact reproduction of a component. Even sub-microscopically small details are copied, so the technique can be used, for example, to make masters for the reproduction of holograms.
The material properties of the product are determined by the properties of the deposited metal, the deposition rate and the plating parameters.
The substrate may be a metal, but also non-conducting substrates such as ceramics, glass, wood, textile or organic material may be used. In these cases the substrate should be made electrically conductive.
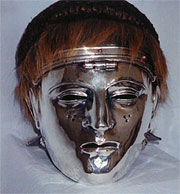 |
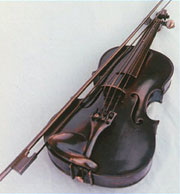 |
Copy of a Roman helmet made by electroforming |
Copy of a violin by electroforming |
Sugar sieves as made by electroforming
Process characteristics
For electroforming a form or mould is needed, on which the metal can be deposited. After deposition the metal is removed from the mould.
Such forms or moulds can be divided into two categories:
- moulds which can be easily separated from the metal and re-used
- moulds which cannot be separated and need to be destroyed
Examples of the first category are moulds for gramophone records; a characteristic example of the second category are moulds for waveguides.
|
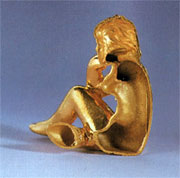 |
Wax model |
Jewel. Where the wax has been removed, a hollow space remains |
Jewel made from a wax mould
When metallic moulds for multiple use are used it is recommended to apply a separation layer. On a stainless steel mould such a separation layer is applied by a dichromate treatment, which causes an oxide layer to form on the steel. On a copper substrate often a thin silver layer is deposited, sometimes treated with sodium iodide.
Pre-treatment
Pre-treatment depends on the mould material. A wax mould is made conductive by application of graphite powder. Other materials are electrochemically treated.
Layer deposition
Layer deposition is carried out by normal electrodeposition, as described for copper or nickel plating. In electroforming it is essential that the metal grows uniformly. Bath composition and deposition parameters have to be carefully selected.
Floating dirt in the bath always causes growth irregularities. Bath filtering and cleaning are therefore necessary.
The current density should be such that no burning is taking place. In some cases specially formed anodes are needed to ensure a constant and uniform layer growth.
In many electroforming applications it is very important that the layers are deposited stress free. Internal stresses in moulds would cause the products to deform during and after separation. Sometimes specific bath compositions are needed.
Copper electroforming
Copper electroforming is used in cases where the special mechanical properties of nickel are not needed. In some cases the properties of electroplated copper, such as the good heat conductivity, make the layer superior to electrodeposited nickel.
In the graphics industry copper electroforms are used for medium to large runs.
Nickel electroforms are often backed up by electroplated copper.
Copper electroforms are extensively used for the production of blown plastic products, such as dolls, and for casting moulds for the fabrication of imitation wood cutting products made by so-called hot melt plastics.
Nickel electroforming
Nickel is one of the most important materials in electroforming. Its price is reasonable. Electroplating of nickel generates coatings with a variety of microhardness, coatings which are corrosion resistant and resistant against a variety of chemical attacks. The practice of nickel electroforming clearly profits from the vast experience in the area of nickel electroplating.
Bath compositions used for nickel electroforming are the Watts nickel bath, the sulphamate nickel bath and the high - speed sulphamate nickel bath.
Recent developments include Ni - Co alloys, used for the fabrication of electroforms and moulds for high temperature application e.g. glass and zinc injection moulding electroforms.
After-treatment
Electroformed components are sometimes not strong or massive enough to be used without damage. In such cases often a copper support is grown on the back side (copper has the advantage that it is a relatively cheap material, and deposited quickly).
Other ways of building a support are using a (low melting temperature) cast metal or a cast resin.
Advantages and disadvantages
Advantages:
- perfect copies
- many different substrate materials are possible
Limitations:
- maximum dimensions depend on the size of the available bath
- labour intensive
- costs are relatively high
Applications
The possible applications of electroforming can be summarized ion the following groups:
- tea canisters
- copies of coins, jewels, natural products
- moulds for e.g. CD’s and records
- electronic components
- forms for blowing plastic parts
- zinc injection moulding forms
- glass electroformsforms.
Jewel, the placing of the mould can be clearly seen.
Electroforming is applied for the fabrication of:
- dental prostheses
- components for instruments including medical instruments
- waveguides for radar installations
- sieves for blood cells, sugar etc
- components for fuel tanks of spacecraft (Apollo rocket)
- electrodes for spark erosion
- sieve print cylinders and pressure plates and ink-jet printer heads in the printing industry
Larger components can be produced by electroforming without problems (e.g. components for the fuel tanks of spacecrafts (Apollo rocket)).
| 
|
| 
|

|

|
|