 |
| | 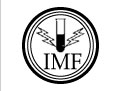 |
 |
 |
|
|
ELECTROLYTIC HARD CHROME
1. Introduction
During electrolytic hard chrome plating, metallic chromium is deposited on a cathodically connected component using direct current and inert (insoluble) anodes. An aqueous solution of chromium acid together with a variety of catalysts is used. It is possible to deposit both bright and matt deposits. As a rule bright deposits are harder.
|
|
Piston rings with a hard chrome coating with a controlled crack pattern to achieve optimum wear resistance and a low coefficient of friction. |
2. Properties
Hard chrome deposits are hard (normally up to 1100 Vickers), wear resistant and can be relatively corrosion resistant; hydraulic rams are exposed to hostile environments and usually remain corrosion-free. In daylight the deposit has a bluish appearance. The corrosion and wear resistance mechanisms are fairly complex but are related to the fineness of the crack pattern, the structure of the deposit and the presence or absence of chromium oxides within the cracks.
3. Substrate
Hard chromium is normally deposited directly onto the base material. Historically it was necessary to put a layer of nickel, copper or bronze between the substrate and the chromium to enhance corrosion resistance; with modern chromium processes this is normally not necessary.
|
|
Engine components essential to fuel combustion are plated with hard chrome and exhibit good wear resistance. |
4. Process characteristics
Hard chrome is deposited from an aqueous solution, just as is the case with decorative chrome. In principle there are three different bath types:
- a chromium acid bath with only sulphuric acid as catalyst
- a bath using fluoride catalysts
- a bath based on organic acids.
In the second and third cases sulphuric acid is the primary catalyst. The last bath enables to use platinised titanium as the anode material.
Different crack patterns in hard chrome:
Micro - cracked chromium from an organic acid catalysed process
Micro - cracked chromium from a bath with fluoride catalysts
Non micro - cracked chromium from a traditional sulphuric acid bath
Pre-Treatment
Great care should be taken in mechanical pre-treatment before hard chrome plating. Machining to the right dimensions and then polishing are the most common pre-treatment.
Before chrome plating the parts are cleaned by hand (larger parts) or by electrolytic degreasing (smaller parts). Often the parts are first etched in the chromium bath or in a separate etching bath (for larger runs).
Plating of hard chrome layers
JJust as is the case in decorative chrome plating, the part is the cathode and plating is done with direct current. The difference is that hard chrome plating uses higher current densities (up to 120 A/dm2 or even higher in some cases – depending on the process).
Hard chrome can be deposited up to several millimeters thickness. Most often thickness is between 30 and 60 µm, after which mechanical treatment (e.g. machining and/or superfinishing) will bring the part to the final dimensions.
The hard chrome baths each produce deposits with specific properties. The organic acid catalysed process generates the highest deposition rate together with intensely micro-cracked chrome layers. This gives the best wear resistance and corrosion resistance.
See standard ISO 6158, also refer to www.bsi-global.com
Post treatment
No specific after treatment other than machining and/or polishing.
5. Advantages & disadvantages
Advantages:
Very wear resistant layer with a potential for good corrosion resistance. Hard chrome is very suitable for the repair of costly and worn machine parts. It is best to deposit hard chrome with somewhat larger dimensions than desired and then machine to the final dimensions. For smaller components in mass production (e.g. engine valves and shock absorber rods) it is quite possible to plate to accurate thicknesses.
Limitations:
- The plating process output is relatively inefficient (14 to 26% theoretical). Not all shapes are easily plated evenly due to limitations of the process (to plate in holes and deep recesses etc.) Sometimes secondary anodes are used for this purpose.
- In order to prevent environmental and health problems hard chrome baths need good environmental control.
6. Applications
On components which are subject to wear such as hydraulic cylinders, mining equipment, shock absorbers, valves, engine parts, spindles, aircraft components, etc.
Hard chromium plated rods. Such cylindrical parts generally have a hard chrome layer between 20 and 75 µm.
|
|
Hard chrome plated and polished parts
Another important application area for hard chrome is where thick coatings (up to a few hundred µm thick) are deposited on parts which require building up and the highest possible wear resistance.
|
|
|
Printing rolls. These rolls are used for high output printing onto “magazine” quality paper. Using electroplated copper, which can be easily engraved, a final layer of wear and ink resistant hard chrome is essential. Many printing factories have their own electroplating department. |
| 
|
| 
|

|

|
|