|
ZINC ELETROPLATING
1. Introduction
Zinc plating is the deposition of zinc from an aqueous solution (electrolyte) of salts using direct current. Electrolytic zinc provides a decorative finish with excellent corrosion resistance. Some company information is recommended, e.g. Anochrome Group, Design Guide, enquiries@anochrome-group.co.uk .
For better corrosion resistance the zinc layer is passivated. This can be in the colour blue, yellow, green or black, depending on the application. In some cases an organic top coat or a sealer is applied.
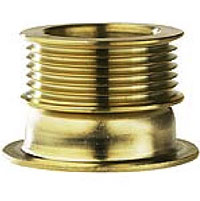 |
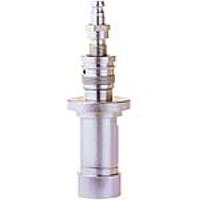 |
Screw capsule, zinc plated with yellow passivation |
Zinc plated part, blue passivation |
Zinc plated channel passivated in several colours
 |
Zinc plated tubing passivated in various colours. |
2. Substrate
The most common substrates material for zinc are carbon steel, unalloyed steel, low alloyed steel and cast iron.
By applying a heat treatment after zinc plating hardened steels can also be zinc plated. The heat treatment is necessary to avoid hydrogen embrittlement.
3. Process characteristics
Zinc plating can be carried out in different aqueous solutions:
- cyanide based zinc baths
- alkaline cyanide-free baths
- acid zinc baths (strong or weak)
Cyanide based zinc baths and alkaline cyanide-free baths give a good thickness distribution of the zinc layer enabling the deposition of zinc on more complex forms.
Large parts such as shopping trolleys, display cabinets as well as smaller parts can be plated on line
Many products are Zinc plated in a line where the products to be treated are suspended.
Smaller objects, such as nuts and bolts are treated in a drum or barrel line. Wire and strip products are treated in reel-to-reel installations.
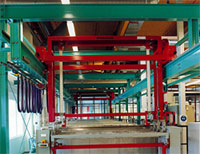 |
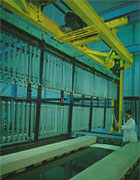 |
These lines can be fully automatic or hand controlled |
Racked components for electroplating |
Pretreatment
Pretreatment depends on the condition of the parts to be plated, and generally encompasses:
- degreasing by immersion
- rinsing
- pickling
- rinsing
- electrolytic degreasing
- rinsing
- zinc plating.
Layer deposition
For obtaining a decorative appearance, the addition of brightening agents is necessary. If no addition agents are used, the layer will have a rough appearance, and a poor corrosion resistance.
Depending on the application, layer thicknesses between 2 and about 40 micrometer are used. See [also NEN-ISO 2081] , DIN 50961 and
www.bsi-global.com
Aftertreatment
After zinc plating the objects are rinsed, and mostly passivated in order to improve the corrosion resistance properties:
- zinc plating
- rinsing
- activation
- passivation
- rinsing
- drying
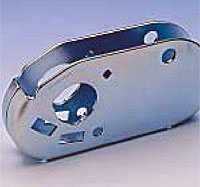 |
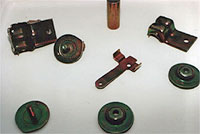 |
Zinc plated and passivated with a bright finish |
Passivated zinc plated parts. The colours range from yellow to green. |
Depending on the layer thickness and the passivation a good to excellent corrosion resistance can be obtained. The colours of the passivation layer can vary: blue, black, yellow and green.
To increase the corrosion resistance a seal can be applied after passivation (on basis of a silicone, acrylate, wax, or a combination of these).
For increased corrosion protection zinc alloys with nickel, manganese, cobalt and/or iron are also electroplated.
Chrome is present in the traditional (Cr vi) passivation layer on zinc. Persistent skin contact can be harmful. As an alternative, chrome-free passivations have been developed.
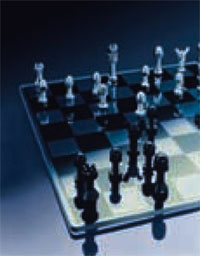 |
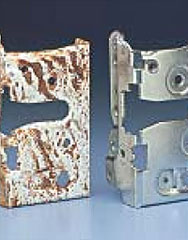 |
Zinc plated chess men passivated for contact with the skin |
Zinc plated automobile parts after 100 h salt spray test. The part at the right has been passivated and sealed with an organic agent. |
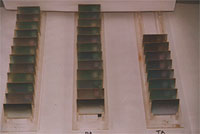 | |
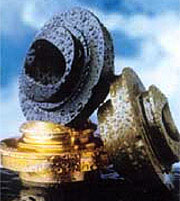 |
Zinc layers with chrome-free passivations are shown on test panels
| |
Zinc plated and passivated parts can be sealed. This seal layer gives extra corrosion protection. |
4. Advantages and disadvantages
Advantages
- good price-quality ratio
- can be easily applied
- decorative finishing
- can be painted
- dimensionally stable
- applicable in several colours
Limitations
- not durable in sea water
- layer thickness varies depending on product shape
Costs
Zinc is a relatively cheap metal and often applied for corrosion protection and decoration.
5. Applications
Zinc layers are often applied for their corrosion resistance and can be found in a large variety of applications e.g.
in automotive applications, camping products, building parts, tooling, shopping trolleys, nuts and bolts, parts for copiers, housings for electrical devices, etc. This is a benign metal and ecologically acceptable but care must be exercised in the choice of passivation processes.
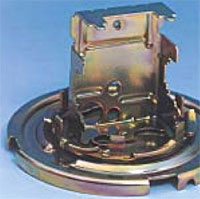 |
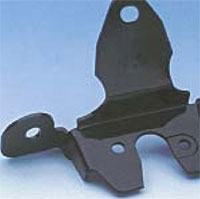 |
Part of a car lamp, zinc plated and passivated for corrosion resistance |
Automotive part, black zinc passivated |
|
|
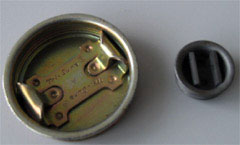 |
Zinc nuts and bolts with different passivation |
Zinc plated capsules from lids of steel barrels. |
| 
|