 |
| | 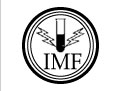 |
 |
 |
|
|
ELECTROLYTIC ZINC ALLOY DEPOSITION
1. Introduction
Electrolytic deposition of zinc alloys is carried out from an aqueous solution of salts (electrolyte) using direct current. Zinc alloy layers can have different compositions:
1) 12% nickel 6- 15%
2) 0,5% iron 0,3-1,0%
3) 1,0% cobalt 0,6-1,2%
4) 1,0% cobalt 0,6-1,2 + 0,5% Iron 0,3-1,0%
The zinc alloy layer is often passivated in order to improve the corrosion resistance which can then be better than similarly treated zinc. This passivation is carried out in the colours yellow, green or black, depending on the application, required corrosion resistance and appearance. In some cases a seal or paint layer is applied. Desirable engineering properties can be obtained.
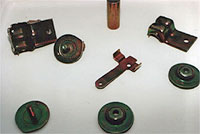
Automotive parts with a passivated zinc-cobalt layer.
2. Electrolytic zinc alloy deposition
Properties
Zinc layers are generally less noble than the underlying material (e.g. steel) and are sacrificed during corrosion. Alloying elements can reduce the corrosion rate, enabling a longer service life without loosing the essential sacrificial function.
A (Cr VI) passivation layer on a zinc alloy plated part is more effective than one on a pure zinc electroplate, so providing longer service life.
Substrates
The most common substrate materials for zinc plating are carbon steel, low alloyed steel and cast iron. On strong steels a bake out may be necessary after electroplating to avoid hydrogen embrittlement.
3. Process characteristics
Electrolytic deposition of zinc alloys can be carried out from different aqueous solutions. We may distinguish between alkaline and weak acid. Alkaline baths give a coating with a very good thickness distribution. Acid alloy baths give a decorative coating.
Pretreatment
Pretreatment strongly depends on the condition of the parts to be plated, and generally involves successively:
- degreasing by immersion
- rinsing
- etching
- rinsing
- electrolytic degreasing
- rinsing
- zinc plating.
Layer deposition
For obtaining a decorative appearance, the addition of brightening agents is necessary. When no addition agents are used, the layer will have a dull appearance.
Depending on the application, layer thickness between 2 and about 40 microns are applied. See also DIN 50962
After treatment
After zinc plating the objects are rinsed, and usually passivated in order to give a desired colour and to enhance their corrosion resistance:
- zinc plating
- rinsing
- activation
- passivation
- rinsing
- drying
Depending on the layer thickness and passivation treatment a thin layer gives a good corrosion protection. The different colours of the passivation layer are black, green, yellow and blue. See also DIN 50962 regarding the corrosion protection. In cases where higher corrosion protection is required, a sealant can be applied after passivation (water - based with a silicone, acrylate wax, sometimes incorporating ceramic particles)
4. Advantages and disadvantages
Advantages
- good price-quality ratio
- easily applied
- decorative finish
- can be painted
- dimensionally stable
- available in several colours
- environmentally friendly and durable
- typically very thin, less than 30 microns
Limitations
- layer thickness distribution depends on product form, but very uniform if applied from an alkaline process
Costs
Zinc is a relatively cheap metal and alloying elements are often needed in only small quantities, so that cost is relatively low.
Applications
Zinc alloy platings are often used for their good corrosion protection. There is a wide variety of applications, including automotive parts, building products, nuts and bolts, brake system components, parts of copiers etc.
Both large and small components can be treated.
For commercial technical information consult www.anochrome.co.uk
A passivated zinc-nickel automotive part
| 
|
| 
|

|

|
|