 |
| | 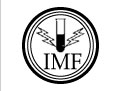 |
 |
 |
|
|
ENAMELLING
An enamel layer is a glass like layer which is very hard and scratch resistant. There are enamels, each kind has specific properties and is used for specific applications. In situations where organic layers are inadequate enamel layers are often applied. The enamel layer is formed during melting of the starting materials.
Enamel layers on steel can be produced in several ways. After initial coating a heat treatment in a furnace always follows.
|
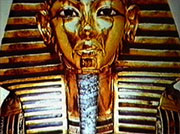 |
Enamelling furnace |
Enamelling was used in early historic times for the coating of jewelry, etcetera |
During melting of the enamel starting materials the enamel layer is formed.
Enamelling is one of the oldest surface treatments, its use going back thousand of years in history.
Properties
Important properties of enamelling layers, which are also the most important advantages are:
- good adhesion to most metals
- colour stable
- easy to clean
- high scratch and wear resistance
- no fouling with micro-organisms
- resistant to high temperatures (450°C)
- resistant to low temperatures (-60°C)
- good resistance to most chemical substances
- electrically isolating
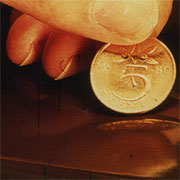 |
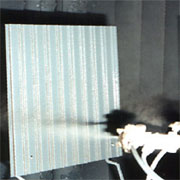 |
Enamel layers can be very scratch resistant. This property is for instance used in enamel counters in bank offices. It is virtually impossible to make a scratch on the counter with a coin. |
The pneumatic spraying of enamel slurry on a heat exchanger plate. These plates are being used in almost all electricity plants in Europe. |
Also in (flue gas) desulphurization plants, enamel plates are being used for their excellent chemical and heat resistance.
The following properties are indications, which may vary depending on the enamel composition. Special enamels, like self-cleaning enamel, cermets and enamel for aluminium may have different properties.
- Density: 2.4 - 3.0 g/cm3
- Elasticitity Modulus: 50 - 80 · 109 Pa
- Elongation strength: 50 - 120 · 106 Pa
- Compression strength: 800 - 1200 · 106 Pa
- Crack formation (on elongation) : 0.12 - 0.3%
- Surface Tension: 170 - 400 mN/m (900°C)
- Expansion coefficient (linear)*: 8 - 12 · 106 / K
- Heat Conduction: 0.5 - 1.0 W / m · K
- Electrical resistance at surface (at 23°C and 50% relative air moisture): > 108 Ω cm
- Electrical resistance at surface (powder coating): > 1013 Ω cm
- Hardness: 4 - 7 Mohs
- Torsion Angle: maximum 180°
- Impact Resistance: 1 - 5 N · m
- Adhesion strength of layer: 1 - 4 N · mm2
- Heat Conduction Coefficient (in z-direction): > 1 W / m · K
- Heat Conduction Coefficient (in xy-direction) **: 20 - 60 W / m · K
- Specific resistance:
- - at room temperature > 1012 Ω · cm
- - at 400°C: 107 to 1012 Ω · cm
- Dielectric Constant (εr): 5 – 10
- Angle of loss (tanδ) : 10-1 - 10-3
* In temperature range 20°C - 100°C
** Depending on the thickness of the plate and the mechanical strength of the enamel layer
*** Depending on the relative air moisture
Further information can be obtained from the Institute of Vitreous Enamellers, www.vitreous-enamel.com Material aspects should also be discussed with specialist enamelling companies.
Substrates
Not all metals can be used as a substrate for enamelling. Most metals however will have alloys suitable for enamelling. We will now present various metals, on which an enamel layer can be deposited.
Steel
Enamelling is less tolerant to the substrate material than is coating with an organic layer. The carbon in the steel may react to form CO2 at higher temperatures. This gas can strongly disrupt the formation of the enamel layer.
|
|
Cross section of an enamel two layer system. Clearly the gas bubbles in the enamel layer can be seen. These bubbles are formed during heat treatment and contain mostly CO. In this case the enamel layer will behave normally. High gas formation will disrupt the normal formation of the layer. |
There are two kinds of steel for enamelling:
- Low carbon steel, with carbon contents of 0,02 to 0,10 %
- Decarburized steel, with carbon contents less than 0,004 %.
The general requirements for steel to receive an enamel layer are described in Eurostandards (EN) 10130 and EN 10209.
In certain cases special standards have been developed (or are being developed) such as DIN 17100 (st 34-2), DIN 17155 (Kesselblech H 1) and SE 613 (heat exchanger plates).
Steel fit for enamelling needs to meet a number of requirements. Depending on the application and the enamelling process, one or more of the following requirements should be met:
- defect free surface
- reactive surface
- resistance to the formation of ‘fish scales’
- deformation resistant
Stainless steel
Only a limited number of stainless steels can be used for enamelling. These are the austenitic chrome-nickel stainless steels of the type 18/8. Chromium present in the alloy will form chromium oxide during firing of the enamel, which is not soluble in the enamel. However, if sufficient nickel is present, such as is the case in austenitic chrome-nickel stainless steels, the disruptive influence of the chromium is compensated. Suitable stainless steels for enamelling are known under the numbers 1.4301 according to DIN 17440 and ACSI 304 and 316.
Cast iron
Cast iron fit for enamelling needs to fulfil a number of requirements, such as a suitable chemical composition, expansion coefficient, surface roughness and shape.
Both cast iron with graphite lamellae and grey nodular cast iron can be enamelled, depending on the chemical composition
To be more specific, the surface of the cast iron needs to be clean and free of:
- pores, cracks, defects and inclusions
- so-called ‘cold-loop’ (sand blasting) inclusions
- inclusions of sulphur, sand, too large graphite inclusions, too much sulfite (MnS or FeS).
Of great importance are: the preparation of the cast iron, and the composition of the sand during casting. Generally the quality of a cast component directly influences the quality of the enamel.
Aluminium
|
|
Enamelling of aluminium coil. Here the enamel slurry is pneumatically sprayed onto the aluminium coil. These coils are used for instance in buildings (partitions).
During the enamelling of aluminium one should take the low melting point (800 to 830°C) into consideration. Firing of standard enamel would require a higher temperature than the melting point of aluminium, therefore special enamels have been developed for aluminium which all have a good chemical resistance. |
Noble metals: silver and gold
The noble metals silver and gold are almost exclusively enamelled for decoration purposes. Since these metals do not oxidize, it is possible to apply the enamel locally. This enables conservation of the original noble metal colour at chosen places.
Process characteristics
The enamelling process has the following steps:
- deposition of the enamel powder or slurry
- drying in case of slurry
- firing
Pretreatment
Pretreatment is comparable to pretreatment in galvanic processing, it depends on the composition of the base material. Pretreatment methods are:
- degreasing
- degreasing and staining
- degreasing, staining and growth of nickel
- sand blasting
Layer formation
The application of an enamel can be compared to painting and powder coating. Enamel is applied as powder or as slurry. The most common application techniques are:
- large runs: electrophoresis and electrostatic spraying (wet or powder)
- small runs: painting, plunging and spraying.
|
|
Electrostatic enamelling with powder in a small furnace
|
Application of organic coatings is quite similar to the application of enamel. Here is an installation for electrophoretic spraying. This technique is very conducive to a good uniform coverage.
|
Drying
Enamel slurries need to be dried after application before firing. The following drying methods are used:
- air drying
- infrared drying
- heat convection drying
Firing
During firing the dry enamel biscuit is transformed into a well adhering, chemical resistant, and hard enamel layer.
Common firing temperatures are:
800 to 870 °C for steel
750 to 800 °C for cast iron
500 to 550 °C for aluminium
For firing chamber furnaces, band furnaces or tunnel furnaces are used.
After treatment
There is no after treatment for enamel after firing.
Advantages and disadvantages
Advantages
- Good adhesion to metals
- Stable colour
- Easy to clean
- High scratch and wear resistance
- No fouling
- Can withstand higher temperatures (450°C)
- Can withstand lower temperatures (-60°C)
- High resistance to chemical attack
- Good electrical isolation
Disadvantages
- Limited impact resistance, especially in comparison with organic coatings
- Danger of ‘fish scale’ formation when unsuitable steel alloys are used; ‘fish scales’ are typical defects, which are caused by gas bubbles
- An enamel coating generally cannot be repaired on site
- Limited flexibility. Local enamelling is generally impossible
- Enamel parts are difficult to join. The design of enamel constructions is following special rules. Ask your enamel company.
Applications
There are a large number of enamel applications. Examples are:
- building facades
- magnetron furnaces
- household appliances
- blackboards in schools
- electrical isolators in heating elements
- heat exchangers in heating devices and electricity plants
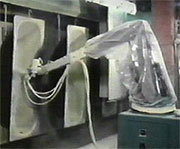 |
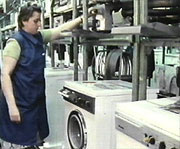 |
The application of an enamel slurry on bath tubs using a robot |
A washing machine with an enamel coating |
|
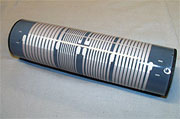 |
Solar collectors using black enamel steel plate (for its good corrosion resistance) |
Enamel heating element |
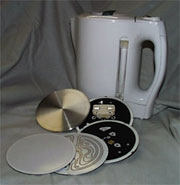
Water boiler. It is possible to make electrically conducting tracks in enamel on an enamel plate. In this way printed circuits with a very high corrosion resistance are fabricated. Also heating elements are made, e.g. in some water boilers.
Requirements
Steel
Steel alloys for enamelling are described in the standard EN 10209. They should have:
- a maximum in carbon content
- a homogeneous surface
- a good resistance to ‘fish scale’ formation
Cast iron
- Minimum thickness 3 mm
- The iron should be recently cast
- Free of contamination
- Free of graphite, sulfides and sulfur
- Free of inclusions, bubbles and pores
Aluminium
Magnesium content not higher than 0,01 %.
Stainless steel
Depending on the application both austenitic (type 18/8) and a number of ferritic alloys can be used.
Copper
Red copper can be enamelled, but the zinc content should be not higher than 5 to 10 wt.% i.e. brass cannot be enamelled.
Silver, Gold and Platinum
Enamelled noble metals are primarily used for art and ornamental objects
| 
|
| 
|

|

|
|