 |
| | 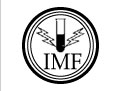 |
 |
 |
|
|
GALVANIZING
Galvanizing is an immersion process, in which steel objects are immersed in molten zinc for a short time at 445 to 465ºC, or are passed through liquid zinc. There are two galvanizing processes:
Continuous galvanizing of steel plate, wire, wire netting and tubes is done in a special installation. Galvanizing of steel strips is the most well known. In this process steel strip of max. 2 m wide is transported through a closed oxidation and reduction furnace into the liquid zinc. In the oxidation and reduction furnace the surface is prepared for the process. The zinc layer on the strip can be between 7 and 30 µm thick.
In discontinuous galvanizing, also called job galvanizing, steel objects to be coated are immersed batchwise in a bath of liquid zinc of 445 to 455°C, after chemical pretreatment of the steel. The layer thickness can vary between 50 and 250 µm depending on the substrate material thickness. In both galvanizing processes a layer system is formed that is alloyed to the steel and, depending on the process rate, this consists of one or more zinc-iron alloy layers, covered by a pure zinc coating.
Both processes are conducted in various variations. Since galvanizing means the deposition of a zinc layer, the requirements for the process should be specified in regulations, standards, quotations, etc.
A galvanized layer protects steel against long time corrosion. If an organic top layer is deposited on the zinc, this is called a duplex system (Zn + organic top layer).
|
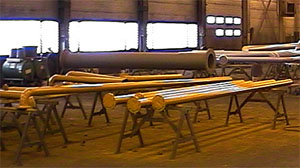 |
Strip of galvanized steel. After zinc deposition also an organic coating is deposited. |
Galvanised products are covered with a duplex layer, in this case a wet paint. Parts of facades and smaller products can be painted in an automatic installation. |
Zinc is deposited during discontinuous galvanising generally with a layer thickness between about 80 and 150 µm. The layer consists of Fe/Zn alloy layers, from the inside out a gamma double layer (21 to 28% Fe), delta (6 to 17% Fe), zeta (5.8 to 6.2 % Fe) and eta (99.9% Zn).
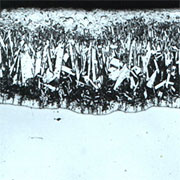 |
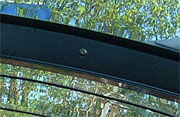 |
Cross section of a galvanized zinc layer. The different alloy layers can be discerned clearly. |
These layers give a very good corrosion protection. After some weeks in humid air an alkali zinc carbonate layer forms on top of the zinc, which somewhat protects the zinc from the environment and improves corrosion resistance. |
Galvanised zinc layers are very impact and wear resistant and are often applied in situations where other layers will not perform due to insufficient impact resistance. So-called reactive steel can lead to very thick alloy layers which are hard and brittle and can lead to delamination.
All galvanized layers will have good adhesion to the substrate.
Galvanizing For more information go to the Galvanizers Association www. Galvanizing.org.uk
Substrate
The substrate generally is steel (construction steel, cast steel or cast iron).
Alloying elements in the steel can influence the deposition rate of the zinc and zinc alloy layers.
In the case of a reactive steel this can lead to an extra thick layer which looks less attractive but will lead to an increased corrosion protection because more zinc is available for self sacrifice. Thick layers however are less suitable in mechanical applications with high loads or for duplex systems, since they look less attractive.
Process characteristics
Discontinuous galvanising: sorting and hanging
Pretreatment
Deposition
After treatment
Removing and categorizing
Pretreatment
As a pretreatment iron or steel parts are degreased and etched. After this a flux of zinc-ammonium chloride is deposited. The purpose of this flux is to remove residual oxide remains so that a good adherence is obtained.
Layer deposition
The molten zinc is heated to 445 – 465C in a steel bath. The material to be galvanized is treated with flux and then immersed in the bath. No air inclusions are permitted. In the bath the molten zinc reacts with the iron. In this reaction several zinc-iron layers are formed. After taking the part out of the bath the remaining zinc droplets are removed.
Before removing the object from the bath the floating zinc oxides are skimmed to the edges of the bath.
These oxides are rapidly formed on the surface of the zinc melt in air. After removing the zinc oxides the object is taken out of the bath.
After treatment
After cooling it is checked whether the layer is unbroken and unwanted droplets and impurities are removed. If needed the zinc layer can be intensively pretreated before deposition of an organic layer (duplex system).
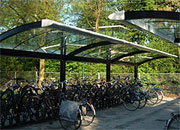
Galvanised bicycle rack with a duplex layer system. In this case the zinc is coated with a powder coating.
Advantages and disadvantages
Advantages:
- Fe/Zn alloy layers are formed from the underlying material by alloying with zinc and as a consequence coatings have good adhesion.
Disadvantages:
- dimensions of the objects are restricted by the zinc bath
- aesthetic requirements can be partly met. The degree of bright crystallization relies on operator experience.
Costs
Costs depend on the composition of the work piece material, and are generally between € 0,25 to € 1,25 per kg product.
Application
Galvanising is a very popular way of protecting iron and steel against corrosion. In modern cars the largest part of the chassis and coachwork is galvanized. In construction and building galvanized steel constructions are applied. Also in the agricultural sector most corrosion protection in constructions such as stables is realized by galvanized steel.
|
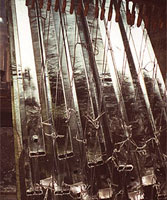 |
Galvanizing of tubes. These tubes are used in building construction and for electrical conduit. |
Galvanised sections used in greenhouses. Hollow profiles are also internally coated. |
On the street lamp posts, garbage cans and lids are galvanized.
Galvanised and powder coated fence. This combination gives a long time corrosion protection.
Steel constructions in an aggressive environment which require a long lifetime, such as bridges, industrial installations etc., are often protected with a duplex layer system.
Deposition of a duplex system on a galvanised construction. In this case a wet coating is deposited on the zinc, consisting of a primer and a top layer
Conditions
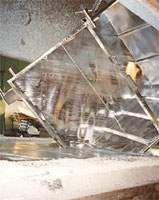
Material thickness and geometry will influence the eventual performance.
Continuous galvanized steel can be deformed for a few months after deposition; discontinuous galvanized steel products should be galvanized after forming.
After treatment (drilling, cutting) will have a negative influence due to uncoated edges. Welding and cutting of galvanized steel should be done with local extractors and/or breathing protection due to welding fumes generated during these processes.
Discontinuous galvanized parts should be adapted to the available bath dimensions. Bath dimensions for galvanizing are generally larger than for any other immersion technique.
Galvanising of a fence. The maximum dimensions of the work piece are determined by the dimensions of the zinc bath.
Barrel or centrifugal galvanizing (a variation of discontinuous galvanizing) is only possible on relative small parts. The parts are placed in a perforated steel barrel, after which the barrel is immersed in the zinc bath. After galvanizing the barrel is rotated quickly so that the excess of zinc is removed.
In steel constructions many galvanized steel bolts are applied in order to warrant a good corrosion resistance. Generally these are larger bolts and nuts. After centrifugal galvanizing the wire is cut.
| 
|
| 
|

|

|
|