 |
| | 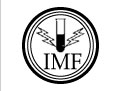 |
 |
 |
|
|
LASER TREATMENT
Surface treatment with a laser beam can be divided into three catagories:
- Laser transformation – A dedicated heat treatment with the aim of transformation hardening
- Laser cladding – Addition of material on the surface and subsequent melting by the laser beam (cladding)
- Laser alloying – Material addition to an alloy, with subsequent remelting.
Principle of the laser process
More information on laser treatment processes can be obtained at:
Include name of one or more UK companies.
Laser Cladding:
During laser cladding, a coating is deposited using a laser beam.
Two types of laser cladding processes can be discerned:
- Welding by injecting powder into the laser beam
- Remelting of earlier deposited layers.
Principle of laser clad equipment with powder injection
Properties
The layer thickness normally is in the order of a few mm.
Properties strongly depend on the substrate and coating choice. For instance, one could choose very hard ceramic layers or corrosion resistant stainless steel layers.
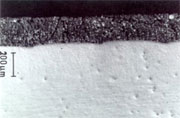 |
|
Cr2 O3 coating with a thickness of ca. 200 mm, deposited using a CO2 laser and treated with a Nd-YAG laser. |
Hardness: depends on the coating material
Maximum temperature during use: depends on substrate and coating material
Wear resistance: depends on the coating material
Toughness: depends on the coating material
Shock resistance: depends on the coating material, process conditions and layer thickness
Corrosion resistance: depends on the coating material.
Laser Cladding , the substrate
The technique is being used on all kinds of steel and cast iron.
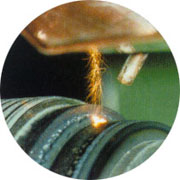
Process characteristics
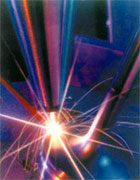 |
|
One can discriminate between a one-step process, and a two-step process. In a one-step process, powder is injected into the laser beam. The powder mixes with the (molten) outer layer of the substrate, so that a relatively homogeneous mixture is obtained. After solidification and cooling the welded layer is formed.
In the two-step process, first a surface layer is deposited by (e.g.) flame spraying. Then the layer is densified, melted, or its adhesion is increased by laser treatment.
The substrate and coating material are selected for the specific application; the coating may be a layer of Fe Cr Al Y or WC or Cr. |
Practice of laser cladding a valve seat.
Pre-treatment
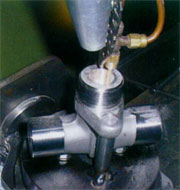 |
|
The surface needs to be clean, and reflection by laser light should be avoided (in order to have a maximum heat input to the part)
Laser cladding of a needle valve. |
Layer deposition
The one- or two-step process may be chosen, depending on material choice and requirements.
|
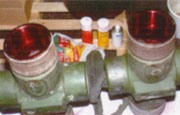 |
Equipment for the laser cladding of seal surfaces |
Inspection of seal surfaces after laser cladding |
After treatment
Normally, machining is not necessary.
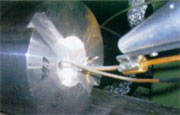 |
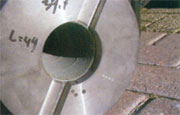 |
Laser cladding of an internal hole |
The cladded hole is ready for after treatment. |
Advantages and disadvantages
Advantages:
- treatment can be carried out very locally
- the options for substrate and clad materials are very wide
Cost
Relatively high, but there are many options for different materials and treatments.
Laser Cladding – Applications
Laser Cladding is a quickly growing technique. Its possibilities are strongly dependent on equipment and product. Equipment providers provide information you about most recent developments.
Both for repair purposes and for the production of new parts there are many options for the use of laser cladding. Some possibilities for application are:
- increase of wear resistance and possibility of local repair of moulds for injection moulding
- repair of turbine blades and valve seats
- inclusion of particles in the laser coating, e.g. WC (tungsten carbide)
- densification of porous coatings
|
|
Laser re - melting of a plasma sprayed shaft. A 30 mm thick shaft, coated with a 0.4 mm Al2O3 coating, has been re - melted using a pulsed laser beam into a 0.15 mm thick layer. The re - melting of the upper part of the coating generates a non - porous surface layer. |
Laser Transformation
Laser surface transformation is the transformation of the outer part of the substrate using heat treatment with a laser beam. The aim is the generation of a hard surface layer.
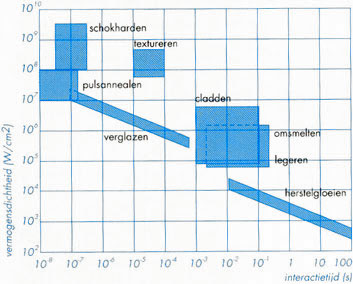 |
|
Overview of the most important application areas of surface treatment by laser (terms in figure: schokharden = shock hardening, textureren = texturising, pusannealzn = puls annealing, cladden = cladding, verglazen = melting into a glass layer, omsmelten = remelting, legeren = alloying, herstelgloeien = annealing) |
Possible applications are:
- Heating to near the melting point, followed by rapid cooling, which leads to material hardening;
- Melting and rapid solidification, leading to a hardness increase;
- Vitrification, caused by melting for a short time and very rapid cooling, causing an amorphous outer layer to be formed;
- Shock hardening, by applying high energy density in a short time, a shock wave is generated in the material surface, to give an improvement of the mechanical properties.
Hardening of a machine part with a high power CW Nd -YAG laser.
Properties
The layer thickness is small: 0.1 to 0.2 mm.
Hardness: depends on the substrate material
Permissible temperature during service: depends on the substrate, for steel substrates a maximum of 175o to 200°C. At higher temperatures, the hardness will substantially decrease.
Wear Resistance; good, but depends on process conditions.
|
|
Laser re - melted surface of a high-temperature construction material. As a result of relatively low heat input during melting high cooling rates can be obtained. This will lead to a fine grained structure with clearly improved properties compared to the original or underlying material. The coarse precipitates in the original coarse-grained casting structure are replaced by a fine-grained structure. |
|
|
Surface area of a laser-hardened coating. In the surface zone the austenite is coarser as a result of grain growth in the surface during heating. The austenite layer at the surface is the result of stabilization of the austenite structure by uptake of carbon from a graphite absorption layer that has been deposited on the component aiming at an increase of coupling with the laser beam. |
Toughness: decreases during laser treatment (as compared to the substrate)
Impact resistance: good, depending on process conditions
Corrosion resistance: good when treated correctly.
Substrates
All metals can be treated with a laser beam. Most applications are found with steel (low and unalloyed) and with cast iron.
Process characteristics
Using a laser beam the surface of the steel can be heated with great accuracy up to about 1300C. This temperature is much higher than with conventional hardening.
The heating time, however, is very short, so that no overheating will take place. Also other metals will be heated up to about 30oC below the melting point. If melting is necessary, locally heating up to 50oC above the melting point is applied.
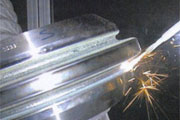 |
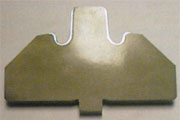 |
Laser hardening of the shaping part of a press tool |
Cross section of a press tool, showing the hardened layer |
Pretreatment
Pretreatment depends on the material and process requirements. Reflection of the laser beam should be taken into account, e.g. with aluminium treated with an infrared laser, reflection may lead to a lower heat input than is required.
Layer deposition
Laser treatment will modify the (structure and properties of) surface layers. Rate of deposition depends on process/product, but can be up to 150 mm/min.
After treatment
After treatment such as machining is possible, but often not needed.
Advantages and disadvantages
Advantages:
- laser treatment is very local
- an optimum system solution can be obtained by selection of substrate and clad material.
- energy input can be controlled in an exact way, so that temperature control of the surface is very precise.
- - distortion as a result of the low heat input normally will not take place, so that machining is not necessary.
Cost
Cost is relatively high, as is the case for many other advanced surface treatments
Applications
Laser hardening is a quickly growing technique, the applications being very dependent on equipment and product. Equipment suppliers will inform you on the latest developments.
|
|
hardheid (HV 300) = hardhead (HV 300), afstand van midden laserspoor = distance from middle of the laser track, oppervlaktetemperatuur in oC = surface temperature in oC, interactietijd in s = interaction time in s, vermogensdichtheid in W/cm2 = power density in W/cm2, brutovermogen in W = gross power in W. |
Comparison of the reproducibility of the hardness of 3 different laser tracks.
Application possibilities: laser transformation hardening of steel and cast iron, e.g. in automobile applications (camshafts, cylinder walls, gearing), roughening of cylinders and rolls (texturing).
|
|
The teeth of this part have been laser hardened. For hardening with a 1200 W CO2-laser the surface has been initially coated with an absorption coating. Parallel tracks with a width of 3 to 4 teeth have been formed with the laser beam. The teeth are almost completely hardened. Under the teeth a transition to the non transformed base material (C45 steel) is visible. |
| 
|
| 
|

|

|
|