 |
| | 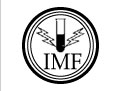 |
 |
 |
|
|
NITRIDING
Introduction
Thermo-chemical surface treatment is a collective name for processes where, at elevated temperatures, elements are introduced into the surface. We will discuss carburising, carbonitriding, nitriding, nitro - carburising, nitrotec, chromising and vanadising.
Nitriding is a thermo-chemical surface treatment in which the surface is enriched with nitrogen.
Nitro-carburising is a variant, where the surface is enriched with both nitrogen and carbon. The process is faster, but the properties are somewhat less favourable than in the case of nitriding.
A variant of Nitro-carburising is known as the ‘Nitrotec’ process. In this process nitriding is followed by an oxidation and seal treatment in order to increase the oxidation resistance.
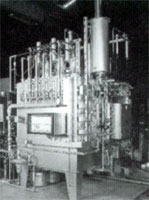
A furnace for Nitro-carburising
The components are heated in suitable ambient containing nitrogen, so that the surface of the material is enriched with nitrogen. The process temperature depends on the steel alloy and can range between 450° and 800°C.
Properties
|
|
The fully treated product has a hard surface. In the surface layer compressive stresses are generated, which make nitrided material very interesting for applications where fatigue strength is needed.
Hardening depth of several steel alloys after nitro-carburising in a salt bath (Term in fig. 1: nitreerdiepte na … (uur) = nitriding depth after … (hour)) |
The typical hardness of nitrided parts is obtained by the formation of nitrides. In unalloyed steel these are Fe4N or Fe2N3. In alloyed steel harder nitrides of alloying elements such as Al N, Cr N and V N are formed.
The hardness is obtained during nitriding. No separate hardening treatment is needed unless during nitriding the temperature has exceeded the transition temperature of the steel (723°C).
|
|
Microscopic cross section of a Nitrotec layer
Iron carbonitride
Reaction layer
Nitrogen
Austenite
Diffusion zone |
|
|
The layer thickness depends on the steel alloy composition; unalloyed steel leads to higher thickness but lower hardness. Alloyed steel forms thinner but harder layers. |
The hardness of the nitrided layer can be up to 1400 HV. For nitro-carburising the maximum hardness is (depending on the alloy composition) between 400 and 1250 HV.
Typical layer thickness:
Nitriding: 0.1 – 2 mm
Nitro-carburising: 0.1 – 1.6 mm
Hardness: 400-1400 HV
Hardening depth: up to about 1.5 mm
Service temperature; up to about 350C
Quality of the surface: hard, pressure resistant, but porous
Wear resistance: good to very good
Toughness: decreases as a result of notch formation in the layer
Impact resistance: limited
Tensile strength: increases with increasing hardness
Corrosion resistance: better than the base material
Substrate
For nitriding low alloyed steel, nitriding steel and tool steel are used
For nitro-carburising unalloyed steel, low alloyed steel, tool steel and cast iron are used.
The choice of steel quality is determined by the required tensile strength of the (nitrided) core, and by the service requirements.
|
|
Hardness required, and hardness distribution from the surface
(Hardheid HV 0.2 = Hardness HV 0.2, Afstand van de oppervlakten (mm) = Distance from the surfaces (mm)) |
|
|
Hardness distribution of some steel alloys.
(gereedschapsstaal = tool steel, hooggelegeerd staal = high alloyed steel, nitreerstaal = nitrided steel, hardhead HV = Hardness HV, diepte onder het oppervlak (mm)= depth under the surface (mm)) |
Examples
C35 - C45: (unalloyed steel with resp. 0.35 and 0.45% Carbon). Wear resistant appliances, machine parts.
16 Mn Cr 5; 34 Cr 4, 41 Cr 4: (low alloyed steel with Manganese and Chromium additions). Machine parts which are subject to fatigue and wear.
30 Cr Mo V9; 36 Cr Ni Mo V7; 34 Cr Al Ni 7: (nitriding steel with strong nitride formers such as Mo, V and Al.). Heavier loaded components, also at high temperatures, moulds for extrusion etc.
GG25; GGG60: (cast iron alloys). Projects subject to high compression forces.
Process characteristics
There are two methods for nitriding:
gas nitriding and plasma nitriding.
In both cases, the furnace is filled with a nitrogen containing gas. The nitrogen diffuses into the surface and forms nitrides with iron and alloying elements such as Al, V, Cr, W and Mo. The process temperature for gas nitriding is 500° to 580°C; the process time is 20 to 90 h.
Plasma nitriding can also be performed at lower temperatures: 450 to 750C, with a process time of 2 to 48 h.
Microscopic cross section (200x) of a nitrided 24 Cr Mo 13 steel. The diffusion zone is visible, but not clearly marked.
|
|
Plasma nitriding, the discharge at the surface.
White zone
Diffusion zone
Steel |
Nitro-carburising has a number of variants: gas, salt bath, powder and plasma nitriding.
The products are brought into the furnace atmosphere, where nitrogen and carbon diffuse into the surface.
During gas nitriding the temperature is 520o to 650oC, the process time is 1 to 6 h.
Salt bath nitriding is done in cyanide containing salt bath. For safety proper precautions should be taken. Bath temperature is around 570oC, process time is 0.5 to 4 h.
After nitro - carburising oxidation must be carried out in air or in a furnace with steam, for 1 h.
Then the material is treated with an organic layer which seals the surface. In this way the layer exhibits a good resistance against atmospheric corrosion.
The growth rate of the layer is 15 to 300 µm per hour. The layer normally consists of two parts, viz. the outer layer (white layer) of 5 to 20 mm, and the diffusion layer of a-Iron with g’-Fe4 N needles, with a thickness of 0.1 to 2.0 mm.
During nitriding the volume of the component increases by 3% of the layer thickness. Adhesion is very good. Care has to be taken to prevent selective growth at the edges.
Layer thickness total: 100-2000 µm
Growth rate of the diffusion zone: 15 to 300 µm per h
Process Temperature: 500 - 580 °C (gas nitriding)
450 - 570°C (plasma nitriding)
Process time: 20-90 h (gas nitriding)
2-48 h (plasma nitriding)
Dimensional deviation: at the surface about 3% of the layer thickness, with selective growth at the edges
Adhesion: very good.
Pre-treatment
The products should be pre-treated, completely clean and smooth. Sharp edges should be avoided and preferably rounded. The material will then be hardened and tempered at a high temperature. Nitriding is then carried out at a temperature well below this tempering temperature.
Layer formation
The gases in the furnace decompose at the surface and nitrogen (plus in some cases carbon) diffuses into the surface. In the outer layer nitrides (and carbides) will be formed. As a result of the high reactivity of the alloying elements the penetration of the nitrogen (and carbon) is limited, so that the layer thickness on nitrided steel is lower than on unalloyed steel.
After treatment
Machining is desirable to remove the outer white layer.
Advantages and disadvantages
Advantages
- The surface is hard and tough, combined with good wear resistance.
- The fatigue strength is increased during nitriding by 30 to 100%
- The corrosion resistance is somewhat higher and with nitriding followed by oxidation much higher
- The resistance against abrasive and adhesive wear is good.
|
|
Influence of surface treatment on corrosion resistance
Prevention of corrosion
Nitro-carburised and degreased
Nitro-carburised and oxidized
Nitrotec
Neutral salt exposure (in hours) |
Disadvantages:
- toughness and impact resistance decrease
- asymmetric products could buckle due to unequal cooling effects
- maximum dimensions are determined by the furnace dimensions
- blind holes cannot be treated during plasma - nitriding.
Costs
These are strongly dependent on the product and process.
Example:
Nitro - carburising: € 0,60 to € 1,15 per kg component mass
Gas nitriding: € 0,90 to € 3,50 per kg component mass
Applications
Nitriding
Machine parts which are subjected to mechanical loads, fatigue or wear such as:
Shock absorbers, piston rods, cylinders, pneumatic/hydraulic tension tools, jacks, drive shafts, gear wheels and moulds.
Hardening takes place during nitriding. A requirement for a good result is that the material is first hardened (before nitriding) so that the core has the proper tensile strength.
Joining of parts can only be done by hard soldering before heat treatment.
|
|
Pinion of a starting motor, treated with Nitrotec C. Better wear resistance and tribological properties. The pinion replaces a sinterbronze-sleeve in the original design. |
Nitro - carburising
Products with a good resistance to adhesive and abrasive wear, to be applied where anti-sticking properties are needed. Nitro - carburising is better than nitriding especially for sliding loads. Maximum service temperature is 350°C.
| 
|
| 
|

|

|
|