 |
| | 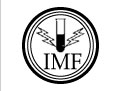 |
 |
 |
|
|
NOBLE, PRECIOUS METAL COATINGS
Introduction
Electroplating with noble metals is a very important technique in modern electronics and microtechnology; traditionally the metals are widely used decoratively and in jewellery.
|
|
Parts with a noble metal coating: silver, gold and rhodium
|
Thermostat with a gold layer
|
|
|
Instrument with silver finish |
Stairs with a gold coating (on board a yacht)
|
| |
Door knob with a gold layer | |
Gold plating
Gold plating is an electrochemical technique where gold or gold alloys are deposited on an electrically conducting substrate from a solution containing noble metal salts using direct current.
Pure gold is a very noble metal and as such 100% oxidation resistant up to the melting temperature. Alloying of gold during electroplating provides layers with very widely differing colours and higher abrasion resistance than pure gold, mostly used for dress jewels and other decorative applications.
For decorative applications electroplate gold, the so-called “Flash Gold” with thickness of about 0.5 μm, is deposited on an intermediate layer of bright nickel. This enables an optimum corrosion resistance, a lasting bright appearance, and a significant cost reduction compared to thicker gold layers.
Gold layers have many technical applications, related to their excellent corrosion resistance, low electrical contact resistance and good electrical and heat conductivity.
Gold layers can be deposited on a large variety of substrates, such as metals, plastics, ceramics and natural materials (leather, wood), in all cases using an intermediate copper or nickel layer.
|
|
Consumer goods with a gold layer
|
A gold plated jewel made by electroforming. The placing of the mould can be clearly recognized.
|
|
|
Baths for noble metal composition |
Jewel made by electroforming |
Silver plating
Silver plating is one of the oldest electroplating techniques, originally patented in 1838.
Silver plating has a very wide application area, notably in the electronic, decorative houseware and cutlery industries
Platinum metals and Rhodium
Electroplating processes have been developed for the Platinum metals, rhodium, platinum and palladium. Ruthenium is used as a grayish plating on expensive products such as pens and pencils. A flash of rhodium is sometimes applied to protect silver plated jewellery from tarnishing.
Rhodium deposits are silver white and very hard, wear resistant and inert in air.
Set of pens with a ruthenium layer
Precious metal coatings – Properties
Gold
Gold coatings are relatively soft. The friction behavior of gold surfaces with other gold surfaces is relatively bad, because of the absence of an oxide layer.
In space applications gold plated components are being used for their good lubrication properties due to the relative low hardness of the gold.
Gold layers thicker than 10 micrometer are free of pores, and as a result the component is very well protected against corrosion attack. The electrical and heat conductivity are very good. Due to the absence of an oxide layer, the solderability is excellent. Gold layers are resistant to most chemicals except cyanide and mixtures of sulfuric and nitrogen acid. They will also be attacked by gases at high temperatures, in atmospheres containing free chlorine. For the improvement of wear resistance and in order to obtain different colours the gold layer is alloyed.
Pure, unalloyed gold has following properties:
Electrical resistance: 2,214 x 10-6 © cm (1,32 x Copper)
Heat conductivity: 3,18 W/cmK, (0,79 x Copper)
Electrochemical equivalent: 2,0435 mg/C (Au I), 0,6812 mg/C (Au III)
Ah weight: 7,3490 g/Ah (Au I), 2,4497 g/Ah (Au III)
Normal- or electrodepotential: 1,692 V (Au I)
Silver
Silver has an attractive white colour and is a relatively dense material. It is soft and ductile and pure silver has the best conductivity for heat and electricity of all metals.
Silver is a noble metal, and does not oxidize in air. Sulfur containing compounds may react to form silver sulfide, giving the silver a brownish appearance.
Pure, unalloyed silver has following properties:
- Electrical resistance 1,587 x 10-6 Ωcm (0,95 x Copper)
- Heat conductivity 4,29 W/cmK, (1,07 x Copper)
- Electrochemical equivalent: 1,1179 mg/C
- Ah weight: 4,0245 g/Ah
- Normal- or electrodepotential: 0,7996 V
Rhodium
Rhodium coatings are very similar to hard chrome layers, since they are very hard and internally stressed after electrolytic deposition. Also very thin layers exhibit a crack pattern similar to that of chrome. They have an extremely high corrosion resistance, better even than platinum.
During deposition of rhodium hydrogen is evolved copiously. Since metals of the Platinum Group easily take up and transfer hydrogen to underlying metal, steel substrates with a hardness higher than 33 Rockwell C should be heat treated after rhodium deposition.
Precious metal Coatings - Substrate
The most common substrate materials are (specially activated) plastic and zinc injection - moulded parts. Also brass, unalloyed, low alloyed steel and aluminium are often used.
Precious metal coatings are often deposited on metal, plastic, ceramic or natural materials such as wood and leather using an intermediate layer, usually copper. Non - electrically conducting substrates such as plastics and glass are first made conductive in this way (also a material such as glass fiber filled epoxy).
(Non-noble) metals are first given a copper layer or a thin gold layer from a ‘gold strike bath’. A gold strike bath is one with an extra quantity of complexant, so that extra cathodic polarization is necessary to deposit the initial layer and displacement is prevented.
A gold plated rose. The rose is made electrically conductive with a copper layer
Precious metal coatings – Process
Process characteristics
The electroplating of precious metals such as gold and gold alloy coatings can be carried out from a variety of aqueous electrolytes. Frequently solutions of cyanides are used.
Baths for the electrodeposition of precious metals and for electroforming
Pre-treatment
Pre-treatment depends on the condition of the components to be treated, and generally contains the following steps:
- Mechanical pretreatment
- Degreasing
- Rinsing
- Activation, possibly by making the substrate electrically conductive
- Rinsing
- Copper or nickel deposition
- Rinsing
Silver, gold and rhodium plating
Deposition
The deposition process is similar to other electrodeposition processes. In view of the cost of noble metals, deposition is carried out under very exact conditions (A/sec.m 2), so that the layer can be deposited with very exact thickness. Care has to be taken to minimise the losses of precious metals during post - plating rinsing.
After treatment
Normally gold layers will not receive an after treatment. Sometimes the layer is polished gently with a very soft tissue. Silver layers are sometimes coated with a very thin layer of rhodium.
Gold plated bathroom tap. The bright appearance is kept by rubbing with a very soft tissue
Advantages and disadvantages
Gold
Gold has many advantages such as an outstanding electrical conductivity and heat conductivity. Its solderability and corrosion/chemical resistance is also very good.
Disadvantages are the high cost, which can fluctuate during the year and the softness of the unalloyed metal.
Silver
Silver also has an outstanding electrical conductivity and heat conductivity.
A disadvantage is that silver can tarnish black in a sulphur containing atmosphere.
Costs
The costs of noble metal layers are relatively high and also dependent on the desired properties.
Precious metal Coatings – Applications
Gold
Gold is applied:
- as infrared reflector in measuring instruments and in some specialist thermal processing equipment
- as conductor for electrical current and contacts; the electrical contact resistance remains low in use
- for printed circuit boards, as the solderability and heat conduction is very good
- in chemical and measuring instruments for its good resistance to chemicals.
For further information refer to www.tecan.co.uk
|
|
Infrared measuring device, consisting of black coloured anodised aluminium and reflectors with an electrolytic gold plate
Gold-cobalt and gold-nickel alloys, also called ‘hard gold’, are often used for watch cases, spectacles, pens etc |
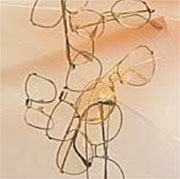 |
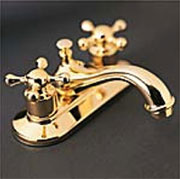 |
Spectacles with very thin gold plating. Since the gold is very thin in such applications, it is porous. Corrosion of the nickel substrate by sweat can cause an allergic reaction |
A gold plated tap |
Gold plated jewels made by electroforming
Silver
Silver is being applied as electroplate in the jewellery industry, including the fabrication of watches. Silver plating is used on a large scale for the making of cheap jewellery. A minimum layer thickness is needed to guarantee a reasonable lifetime.
A special branch is the manufacturing of souvenirs, like pins, little windmills and wooden shoes, bracelet charms where silver plating makes the souvenirs more attractive, and where the requirements for layer thickness are minimal.
The cutlery industry, including the manufacturing of tableware such as bowls and dishes, has more strict requirements, a "30 - year plate" corresponding roughly to a 30μm thickness.
Silver ornaments
|
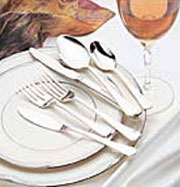 |
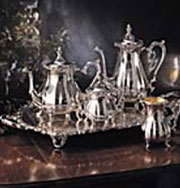 |
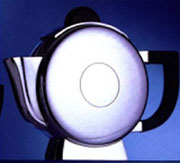 |
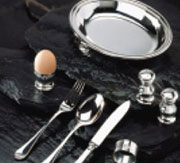 |
|
Several household products |
|
Technical applications of silver plating are very frequent. Due to its good electrical conductivity silver is very often applied in electrical and electronic applications. Silver plating is used for of high frequency applications, since high frequency currents are surface phenomena. High purity deposits are necessary, to maximise the conductivity.
Silver plated contact pens
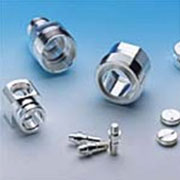
Silver plated parts for electronic applications
In times of high gold prices, silver is used as a replacement for gold in electronic industry, in cases where the adverse properties of silver, such as diffusion, discolouring and changes in contact resistance arte not crucial.
The good reflectance of silver is used in the manufacturing of reflectors, mainly for instrument applications. For technical applications, such as reflectors in car lamps, other techniques have become available, such as the vacuum deposition of aluminum (see PVD).
In chemical instruments silver is often used for its high resistance to a number of chemicals, e.g. in concentrated alkaline solutions.
Thin silver platings are used as substrate for lead-tin and lead-indium sliding bearings.
Silver platings are sometimes used as a release agent for heat resistant metal parts, e.g. in turbines and sealers in nuclear reactors.
Rhodium
Rhodium layers are applied for their silver-white colour, their good hardness and wear resistance and their inertness in air, in two groups of applications:
- as wear resistant layer in electric and electronic applications. Here silver is often covered with a colour - stable wear resistant layer of rhodium (phosphate-rhodium baths give a whiter colour, sulfate baths a more grey appearance of the plating)
- other applications in electronics are sliding contacts in mechanical telephones and in the collectors of high speed electrical generators, used in aerospace (gold-rhodium sandwich). Also heavily loaded contacts for interface cards are plated with rhodium.
Silver plated parts covered by rhodium
Precious metal Coatings – Conditions
The dimensions of parts to be coated depend on the available bath size. Gold plating is very costly. In order to minimize costs, techniques for the local deposition of gold have been developed. These techniques are called ‘selective plating’. The direct deposition of gold on non-noble metals is difficult. Often an intermediate copper layer or a gold ‘strike’ is used.
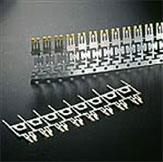
Electronic components with gold contact surfaces. These components are plated in Reel to Reel machines. The local deposition of gold can be clearly discerned.
| 
|
| 
|

|

|
|