 |
| | 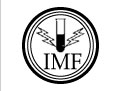 |
 |
 |
|
|
PLATING OF PLASTICS
Introduction
The technique of plastic plating has been applied increasingly in the last decade. The use of plastics is attractive because of the dimensional freedom, the wear resistance of modern polymers and the growing industrial demands for weight reduction.
Properties
Plastics are being produced in a great variety, with many different technical properties.
Decorative plating of plastics as well as functional plating are of growing importance. Most plateable plastics are of the ABS type (Acrylonitrile /Butadiene-Styrene), since these give the least problems. Also mixtures of ABS/Polycarbonate are popular.
Generally, the more inert (resistant to attack) the polymer surface, the more difficult it is to plate the polymer with optimum adhesion (> 1N/mm2). In the case of ABS plastics, optimum adherence is achieved mechanically by a ‘button’ effect. In case of more inert polymers the adherence is more adsorption based.
Substrate
The quality of the injection moulding process (of a polymer part) is very important for the success of plating. ABS without pigments generally gives the best success.
Process characteristics
In order to be able to electroplate plastics, the surface should be ‘roughened’ and metallised, usually with palladium, sometimes with silver. Then, in the conventional plating of plastics, a chemical (electroless) copper or nickel layer is deposited. This renders the plastic sufficiently electrically conductive for the electroplating process.
It is also possible to “directly metallise” the plastic, so that an electroless intermediate layer is no longer necessary. This is better for the process stability.
Pretreatment
The substrate should be absolutely free of grease and oils. For conventional plastic plating the following pretreatment steps are necessary:
- etching and roughening (chromium/sulfuric acid at ~65C)
- rinsing
- chromium reduction
- rinsing
- activation (special Pd solution)
- reduction
- rinsing
- electroless nickel deposition
- rinsing
- Ni strike
- Rinsing
- Electrolytic copper deposition
- Rinsing, if needed activation of surface
- Electrolytic nickel deposition
- Rinsing
- Electrolytic chrome or other material.
Layer deposition
For metallic layer deposition, see the description at the specific subjects: electrolytic nickel/chrome etc. See also ISO 4525.2
No specific after treatment
Advantages and disadvantages
Advantages:
- due to the presence of a bright copper layer very nice decorative layers can be produced
- almost all electroplated coatings are possible, enabling good corrosion resistance
- especially for automotive applications the combination of low weight/good corrosion protection and decoration is very attractive
Disadvantages/Limitations:
- The end result is very dependent on the composition of the plastic and quality of the plastic surface
- Costs vary depending on the number of process steps and desired layer thickness.
Applications
There are many decorative applications, where there is metallisation with copper, nickel, chrome, or possibly gold or another noble metal and a growing number of applications are found in automotive, sanitary ware, and household appliances.
An example of a functional application is the metallisation of plastics in order to prevent disturbance of the environment by electromagnetic radiation (“EMI”), i.e. the housing of mobile phones and other products which contain electronic components.
Plating of printed circuit boards
Refer to www.instct.org
| 
|
| 
|

|

|
|