 |
| | 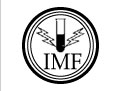 |
 |
 |
|
|
SOL-GEL
In sol-gel technology three basic techniques for thin film deposition can be discerned: dipping, spinning and spraying. Several variants of these are often described as separate techniques e.g. for spraying these are :
- conventional air spraying
- HVLP spraying
- electrostatic spraying
Sol-gel is a versatile technology in which chemical suspensions are used to produce ceramics and glass. Nowadays, the technology has regained interest since it can be used to manufacture - in a relatively cheap way – thin films, fibres, powders and porous membranes. Also attractive is the potential to realise unusual material compositions.
In sol-gel technology a liquid reactive agent is converted into an end product using chemical and thermal processes. The agent is always a liquid with reactive additions (A ‘sol’ is a colloidal suspension).
When a sol is converted to a gel polymerization takes place as a result of evaporation and catalytic reactions. Finally a ‘gel’ is formed, which basically is a solid state network in a liquid. After drying and firing the gel, a glass or ceramic material is obtained, either as a thin inorganic layer or as a body with a high density or as a very porous aerogel.
It is possible to colour the layer by adding a pigment or molecular solution of a colouring agent to the starting material.
After drying and firing of a gel a glass or ceramic compact form is obtained.
Sol-gel – More Information
Sol-Gel technology for thin films, fibres, preforms, electronics and specialty shapes. Edited by Lisa C. Klein, Center for Ceramics Research, College of Engineering. Rutgers- The State University of New Jersey, Piscataway, New Jersey (USA), 1988.
The Physics and Chemistry of Sol-Gel Processing, Edited by Brinker and Sherrer. Academic Press, 1990.
Introduction to Sol-Gel Processing, Edited by Alain C. Pierre and Lisa Klein, Kluwer, Academic Publishers, 1999
Sol-Gel Materials Chemistry and Applications. John. D. Wright (University of Kent, Canterbury,UK) and Nico A. J. M. Sommerdijk (Eindhoven University of Technology, The Netherlands). Gordon and Breach Science Publishers, 2001 (ISBN 90-5699-326-7)
Process Characteristics
The most conventional processes are those which use oxides as a starting material, e.g. tetra-ethoxysilane or tetra-ethylorthosilicate (TEOS) which form Si O2. Other oxide layers are Ti O2, Zr O2 and W O3.
Dipping
In DIPPING the substrate is immersed in a liquid and pulled out with a defined rate. The desired temperature and other conditions are controlled.
This technique is used on an industrial scale for the deposition of anti-reflex (AR) coatings on flat glass substrates.
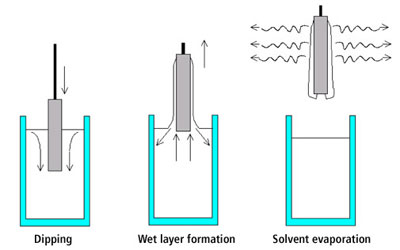
Spinning
SPINNING is characterized by the rotation of the substrate around an axis perpendicular to the plane on which the layer is deposited.
Layer thicknesses of 0.4 to 10 micrometer are not unusual in this deposition technique.
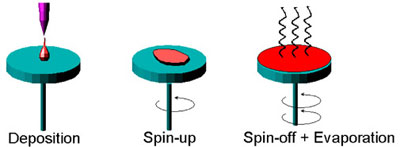
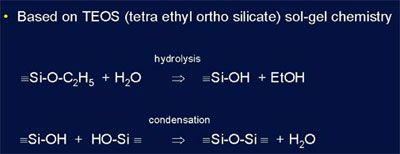
Spraying
SPRAYING is in widespread use for the deposition of organic layers, e.g. paints.
A spraying machine for the spraying of glass substrates with a sol
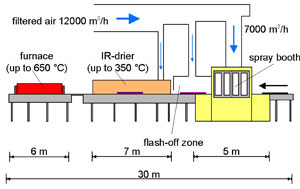
Schematic figure of the complete production process: after spraying the product will be dried and fired.
Spraying is very suitable to deposit layers on 3-D products.
In this base technique, 3 processes can be discerned, depending on the way how droplets are formed:
Conventional Air Spraying, HVLP (High Volume Low Pressure) and Electrostatic Spraying.
The last 2 techniques show a higher transfer yield of the starting material. Also spraying systems are sometimes equipped with a rotating spray unit, a so-called ‘high-speed rotary bell’.
When the surface is hot, so that the reactive starting agent does not reach the surface as a liquid, but as a gas, this is called Aerosol CVD or Spray Pyrolysis.
After spraying the following process steps are drying and heating.
Application
Sol-gel technology is used for a wide range of applications:
Spinning is used to deposit anti-reflection layers on TV screens. In the picture left we see the deposition of the liquid by spinning, after which the system is dried, as can be seen in the picture at the right.
A large variety of substrate materials is being used, e.g. plastics, metal and glass.
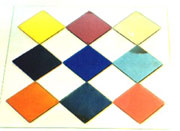 |
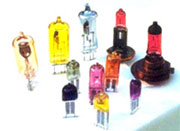 |
In sol-gel technology it is possible to realize colours by adding colouring agents to the sol. |
By depositing a noble metal-colloid (consisting of an inorganic sol-gel) on halogen lamps a very nice decorative effect is obtained. |
In these pictures the same steel alloys can be seen after long treatment in a salt spray test. The left samples were not coated, the samples on the right were coated with a protective layer, applied by sol-gel technology. The corrosion of the coated samples is much less.
For so-called self cleaning surfaces Ti O2 (titanium dioxide) is a well-known coating, which removes all organic compounds by photo catalytic cracking.
The left of the door surface is dirt repellant. This is due to a sol-gel layer.
One of the promises of sol-gel technology is the protection of polymer surfaces to make them more scratch resistant. This is already extensively used on polymer spectacle glasses. Also coloured layers on plastic, glass and light sensitive layers on foils are possible.
Spectacle glasses of which the left one is covered by a scratch resistant layer of silicon oxide by dipping. The covered glass is 5 times better resistant against scratching.
Coloured spectacle glasses made with sol-gel spinning
A plastic foil covered by a light sensitive layer by spraying.
Often hybrid compositions are used – organic/inorganic material – e.g. Si O2 (quartz) in an acrylate network. The properties of the organic and the inorganic phase are mixed in this way, enabling very interesting material properties.
| 
|
| 
|

|

|
|