 |
| | 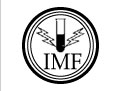 |
 |
 |
|
|
WET PROCESSING
The Electroplating process
Electroplating is normally carried out in aqueous solutions of acids, bases and salts (electrolytes) at temperatures varying between room temperature and 60°C (depending on the process chosen).
The metal salt, which is converted into the metal coating, is present in the electrolyte solution. This solution is in a container, where the anodes – consisting of the metal to be plated on the substrate, or an inert material – are suspended in the solution.
The cathode, which is the component to be plated, is suspended in front of the anodes. Anodes and cathodes are connected to a direct current source which discharges the metal ions to be incorporated in the growing cathode layer. In most cases the material of the anode is dissolved, maintaining the concentration of metal ions in the solution.
In some cases inert anodes are used and the electrolyte must be replenished. The metals are added to the solution in the form of soluble metal salts. Also organic substances may be added to the electrolyte, to influence the layer formation and quality (e.g. "brighteners", "levelers" and "stress relievers").
Very occasionally electroplating is carried out in non-aqueous solutions or ionic melts. The reader is refered to the literature of R&D. (see Transactions of the IMF, Vol 86, p 196-240)
Methods of Electroplating
For each different metal the deposit properties are influenced by varying the addition of organic compounds, metal salts, the electrolyte composition, also by the temperature and current densities applied. Which combination of variables is used depends on the metal to be deposited and on the required functionality of the component, e.g. corrosion resistance, hardness, wear resistance, colour, brightness, solderability, etc. Very occasionally electroplating is carried out in non aqueous (but conductive) solutions or organic melts.
Electroplating is an economical way of satisfying many industrial requirements, e.g. one kilogram of zinc will protect 1000kg of nuts and bolts against corrosion. For economic reasons electrolytes are usually formulated to comply with the requirements of as many clients as possible.
The following main electrolytic processes can be distinguished;
- DC electroplating processes where the components are connected to the negative electrode
- DC electrolytic processes where the polarity is regularly changed during a very short period of time ("pulse plating")
- DC electrolytic processes where the components are connected to the positive electrode ("anodising")
- Processes where the metal ions are discharged and deposited by chemical reduction, without using an external power source. (autocatalytic, or "electroless " plating)
- Displacement reactions
- Brush plating
For electroplating, it is necessary to use a pretreatment and an after- treatment and rinsing is necessary between each (wet) process step.
Pretreatment. This normally takes place in the following sequence;
- Thermal pretreatment (if any)
- Mechanical pretreatment, such as machining, grit blasting, polishing, etc.
- Chemical/electrolytic pretreatment, such as degreasing, cleaning and activating, etc.
After-treatment. This may involve conversion coating, whereby the corrosion resistance is enhanced by chemical conversion of the outermost surface to a coherent oxide.
Rinsing and drying. Sometimes a final heat treatment may be applied, for stress relief or to remove any hydrogen absorbed in depositing on susceptible substrates. Alloy electroplate may be subject to special thermal processing.
Electroforming
Electroforming This electroplating technique enables the fabrication of free standing components which cannot be made economically by other techniques, such as machining or casting; it enables precise replication.
Electroless processes
hese are processes without an external power source, involving autocatalytic deposition by chemical reduction. The most important example of this is electroless nickel deposition. Electroless processes require activation of the base material which does not itself need to be electrically conductive, so that it is often used to provide a metal surface on plastic substrates.
Electroless metal layers are deposited without an external power source, the drive is a chemical reaction in the solution, usually the metal is deposited by nascent hydrogen formed at catalytic surface sites. This reaction is ‘auto-catalytic’ in most cases, which means that it is self-sustaining. Electroless nickel is often used as matrix material for the growth of composite layers. These are coatings where a dispersed phase (mostly small particles) is built into the matrix to provide special mechanical properties.
Displacement deposits involve the dissolution of active substrate surfaces with the deposition of an equivalent of less active (more "noble") metal from the electrolyte. Once the substrate is covered by the less active metal the reaction ceases.A displacement reaction is essential for electroplating on to aluminium and its alloys. Here a zinc underlayer is usually formed by displacement, for further electrodeposition.
Heat treatment of electroless nickel layers
Electroless nickel is metallurgically complex and heat treatment is often carried out to improve the adhesion or to modify properties needed for a specific application. As a result of heat treatment, properties such as corrosion resistance, wear resistance and ductility can be improved.
Some products with a decorative electroplating layer giving protection against corrosion.
: Zinc coated fasteners; the zinc coating protects against corrosion.
One hundred mg gold protects 5000 electrical contacts against corrosion and gives a good electrical conductivity.
Objects are often coated with a thin gold layer for decorative purposes.
In modern cars between 2000 and 3000 electroplated components are being used. 15 kg nuts and bolts are plated with zinc.
In modern cars there are between 2000 and 3000 electroplated components. A large number of these car components are electroplated for functional purposes and to give corrosion resistance. e.g. 15 kg of nuts and bolts are plated with zinc (see Fig 5).
In a modern car there are some 18 m2 of printed circuit boards and these are fabricated using electroplating. The electronic systems are responsible for about 20% of the car costs.
In a modern aeroplane, such as Airbus, there are about 2 million electroplated components and several hundred m2 of printed circuit boards.
Small parts plated with zinc
Electronic components, which can only be fabricated using electroplating.
An ‘automatic electroplating bath’, where the electroplating process steps are programmed.
The jigging of components to be zinc plated in an automatic electroplating line.
Gold plated jewellery made by electroforming
Machined parts with an electroless nickel layer
Modern bath for electroless nickel.
Extruded aluminium parts with an electroless nickel layer
| 
|
| 
|

|

|
|