 |
| | 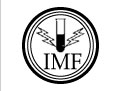 |
 |
 |
|
|
PRINCIPAL TREATMENT TECHNIQUES
Electroplating and Electroless plating
Electroplating
Electroplating is the electrolytic deposition of an adhering (metal) layer on an electrode, aiming to give surface properties which differ from those of the base material. For instance, a very thin metal layer (thinner than a human hair) is often a very effective protection against corrosion. The process of electroplating is described briefly; examples of specific applications are also given there.
Electroplating processes using an external power source:
Electroless processes:
Processes combining electroplating and electroless plating:
Aluminium and its alloys acquire tenacious and protective oxide layers in air. The formation, thickness and useful properties of these layers can be optimised by producing them anodically. Similar treatments are used for magnesium, titanium and zinc, but some 95% of all anodised material is aluminium.
Thermochemical Surface Treatments
These are processes where, at elevated temperatures, alloying elements are introduced in to the substrate surface. They are often refered to as Pack Processing.
This is applied to steel. In a furnace treatment the surface of low-carbon steel is enriched with carbon by diffusion from a surrounding medium. This produces a hard surface on a substrate that remains tough. Carbonitriding involves the co-diffusion of nitrogen, resulting in a thinner surface layer.
In nitriding the furnace is filled with a nitrogen containing gas, the process may be applied to low alloyed steel and tool steel and to steels containing strong nitride formers (eg Mo, V, Al). Plasma nitriding involves lower furnace temperatures and shorter process time than carburising.
Boronising (Boriding)
Boronising involves the diffusion of the element from a surrounding medium to form a compound layer of metallic boride in the substrate surface. Temperatures of 800-1000ºC are applied for some hours and the technique is used to produce abrasion resistant surfaces on titanium-based and cobalt based alloys and on a restricted range of steels.
Laser processing is associated with very high rates of heat input. This is exploited in three types of surface treatment
- Laser transformation i.e. heat treatment
- Laser cladding
- Laser alloying
A long -established process in which zinc is diffused to form a corrosion resistant layer especially on small instrument components made of iron and steel.
An enamel is a glassy layer, normally highly resistant to contaminants, wear and temperatures between -60ºC and 450ºC. Its application involves a furnace treatment. Enamels can be applied to a good range of metallic substrates.
Hot dip galvanizing provides a robust alternative to zinc electroplate ("electrogalvanizing").
Physical vapour deposition (PVD) includes a range of processes in which vapour phase species, atoms or ions are derived from solid or liquid target materials by evaporation or sputtering. Coatings are formed from these species by simple condensation or after their activation, eg in a plasma. In a third PVD process the potential of the workpiece is adjusted to make it the cathode in a glow discharge. Chemical Vapour Deposition (CVD) is the deposition of coatings on heated surfaces from their chemical reaction with the ambient gases. This may be combined with radio-frequency glow discharge reaction enhancement. Currently there is conciderable interest in the nature and application of diamond-like coatings
Shot peening. Mechanical plating.
| 
|
| 
|

|

|
|